Valve body manufacturing method
A manufacturing method and valve body technology, applied in the field of valve body manufacturing, can solve problems such as increased equipment cost, energy waste, and limited material performance of the valve body, so as to reduce equipment and production costs, reduce pollution and energy consumption, The effect of improving market competitiveness
- Summary
- Abstract
- Description
- Claims
- Application Information
AI Technical Summary
Problems solved by technology
Method used
Image
Examples
Embodiment Construction
[0015] refer to figure 1 , a manufacturing method of a valve body, comprising the following steps:
[0016] The first step is to heat-melt and extrude the metal raw material into a long profile; this step can be carried out in the existing profile production plant, and the valve body manufacturer does not need to be equipped with additional heat treatment equipment, which reduces equipment and costs. The production cost is improved, the production efficiency is improved, and the pollution and energy consumption are reduced at the same time, which is energy-saving and environmentally friendly.
[0017] In the second step, the profile is cut into several sections of blanks. The shape of the blanks matches the shape of the valve body and is slightly larger than the valve body, which is convenient for processing and can also reduce the waste of materials.
[0018] The third step is to grind and drill the blank to obtain the valve body, and a polishing process can also be added to...
PUM
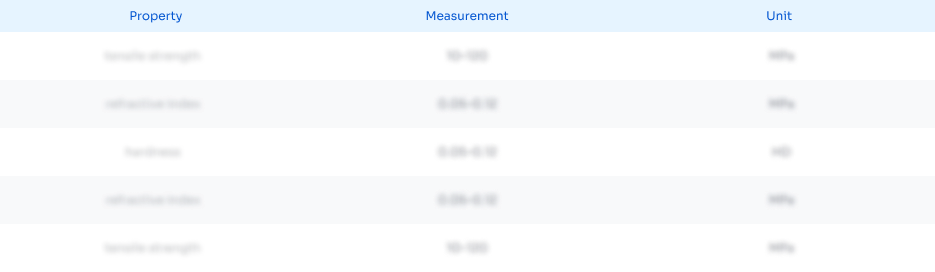
Abstract
Description
Claims
Application Information

- Generate Ideas
- Intellectual Property
- Life Sciences
- Materials
- Tech Scout
- Unparalleled Data Quality
- Higher Quality Content
- 60% Fewer Hallucinations
Browse by: Latest US Patents, China's latest patents, Technical Efficacy Thesaurus, Application Domain, Technology Topic, Popular Technical Reports.
© 2025 PatSnap. All rights reserved.Legal|Privacy policy|Modern Slavery Act Transparency Statement|Sitemap|About US| Contact US: help@patsnap.com