A process for catalytic gasification of carbonaceous feedstock
A raw material and carbonaceous technology, applied in the field of synthesis gas preparation, can solve the problem of not providing catalyst, etc., and achieve the effect of enhancing the purity and reducing the circulation rate
- Summary
- Abstract
- Description
- Claims
- Application Information
AI Technical Summary
Problems solved by technology
Method used
Image
Examples
example 1
[0082] Three different feedstock-catalyst mixing methods were considered in these experiments, namely direct mixing, impregnation, and incipient wetness impregnation. The direct mixing method was used in Experiment 1 and Experiment 2, where dried coke (particle size less than 73 microns) was directly mixed with the catalyst and dried at 105°C temperature and atmospheric pressure for 12 hours. The impregnation method was used in Experiments 3 and 4, in which a specified amount of catalyst was dissolved in 200 ml of water, and 10 grams (gms) of dried petroleum coke was dispersed into this water solvent of the catalyst, and heated at a temperature of 80 °C and Drying was carried out for 24 hours at a comparative pressure and for 12 hours at a temperature of 105° C. and atmospheric pressure. In experiments 5 to 8, the supported catalysts were prepared using the incipient wetness method. In this case, the desired amount of catalyst is dissolved in water corresponding to the pore v...
example 2
[0086] A series of experiments were performed at laboratory scale to determine the catalytic activity of the catalysts as suggested in this disclosure. Petroleum coke gasification experiments were carried out in a fixed-bed reactor to investigate the catalytic activity of the proposed catalysts. The experimental setup consisted of a steam generator and a vertical tubular reactor (25.4 mm (1 in) inner diameter, 254 mm (10 in) long) heated by an electric furnace. Once the reactor is loaded with a given weight of feedstock mixture, the feedstock mixture can be heated to the desired temperature under a flow of inert gas (nitrogen). Once the gasification temperature is reached, steam can be introduced into the reactor at a given flow rate. The product gas was collected and analyzed by gas chromatography (GC). Once the desired run time is reached, the flow of steam into the reactor can be shut off. The unconverted carbon is combusted with air and the total combustion product gas ...
example 3
[0091] A series of experiments were performed to investigate the effect of catalyst to petroleum coke ratio on conversion / gasification. Catalysts prepared as described in Examples 1 and 5 were used in these experiments. Carry out the experiment on the same experimental apparatus described in example 2, adopt the ratio of different catalyst coke, as 1:2,1:4,1:8,1:10,1:12,1:20,1: 25, 1:30, 1:40 and 1:50. Table 3 shows that the conversion increases with the ratio of catalyst to coke. It can be seen that the gasification rate increases with the ratio of catalyst to coke, which leads to a decrease in the residence time required for complete conversion. In particular, in fluidized bed gasifiers, residence time plays a major role in the conversion of feedstock. In a two-bed system, maximum conversion can be expected at minimum residence time and highest catalyst loading. This experiment conclusively demonstrates that alkali metal catalysts must not only function as individual par...
PUM
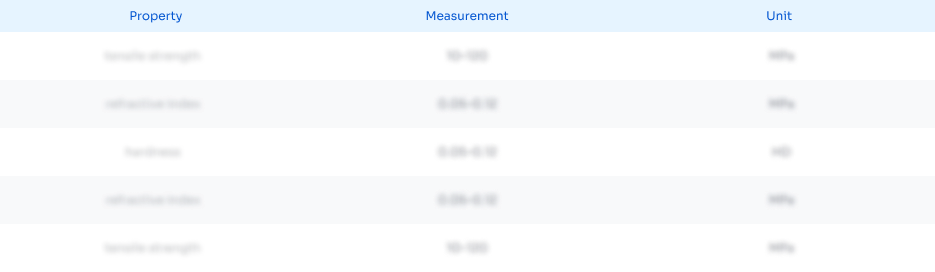
Abstract
Description
Claims
Application Information

- R&D
- Intellectual Property
- Life Sciences
- Materials
- Tech Scout
- Unparalleled Data Quality
- Higher Quality Content
- 60% Fewer Hallucinations
Browse by: Latest US Patents, China's latest patents, Technical Efficacy Thesaurus, Application Domain, Technology Topic, Popular Technical Reports.
© 2025 PatSnap. All rights reserved.Legal|Privacy policy|Modern Slavery Act Transparency Statement|Sitemap|About US| Contact US: help@patsnap.com