Experiment method for measuring asynchronous curing degree distribution of transparent resin material
A technology of transparent resin and experimental method, which is applied in the direction of material analysis, measuring device, and material analysis through optical means, which can solve the problems of inability to monitor uneven curing and simultaneous curing of layers, so as to reduce the interference of curing, The result is precise effect
- Summary
- Abstract
- Description
- Claims
- Application Information
AI Technical Summary
Problems solved by technology
Method used
Image
Examples
Embodiment Construction
[0019] The specific structure, working principle and working process of the present invention will be further described below in conjunction with the accompanying drawings, but the protection scope of the present invention should not be limited by this.
[0020] figure 1 It is a schematic diagram of the structure and principle of the device for measuring the curing degree distribution of transparent resin materials. The device includes a laser, a beam expander, a convex lens 1, a material to be measured, a grating 1, a grating 2, a convex lens 2, a diaphragm, a CCD camera, and a computer; the light emitted by the laser passes through the beam expander to form a coherent light source and then The parallel light formed by the convex lens 1 enters the heating furnace, providing parallel incident coherent light source for the material to be tested; the material to be tested is placed in the heating furnace, and the vacuum pump is connected to the heating furnace to provide a vacuu...
PUM
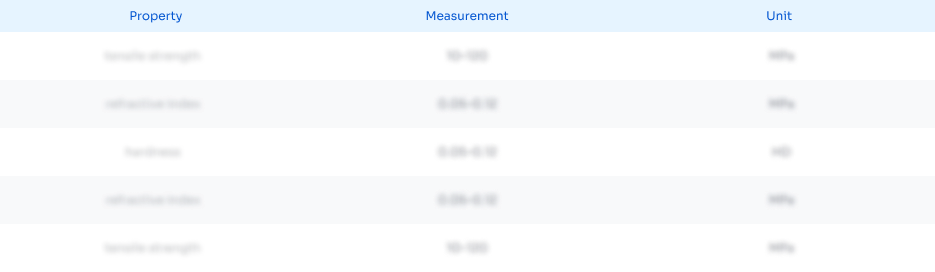
Abstract
Description
Claims
Application Information

- R&D
- Intellectual Property
- Life Sciences
- Materials
- Tech Scout
- Unparalleled Data Quality
- Higher Quality Content
- 60% Fewer Hallucinations
Browse by: Latest US Patents, China's latest patents, Technical Efficacy Thesaurus, Application Domain, Technology Topic, Popular Technical Reports.
© 2025 PatSnap. All rights reserved.Legal|Privacy policy|Modern Slavery Act Transparency Statement|Sitemap|About US| Contact US: help@patsnap.com