A process for reducing formaldehyde of medium and high density fiberboard
A technology of high-density fiberboard and fiberboard, which is applied in the direction of manufacturing tools, wood processing equipment, wood treatment, etc., can solve the problems that cannot be removed by hot pressing of fiberboard, increase the water absorption expansion rate of fiberboard, reduce moisture resistance, etc., and shorten the production cycle , short health preservation time, and the effect of reducing treatment costs
- Summary
- Abstract
- Description
- Claims
- Application Information
AI Technical Summary
Problems solved by technology
Method used
Image
Examples
Embodiment 1
[0059] A process for reducing aldehydes of medium and high density fiberboards, comprising the following steps:
[0060] 1) Vacuum sealing: Place 50 sheets of medium and high-density fiberboards with a density of 0.82g / cm³ and an initial formaldehyde content of 15mg / 100g evenly on the display rack 2, with an interval of 15mm between each fiberboard, and then carry them through the track 3 Push the trolley of the display rack 2 into the vacuum box 1, close the door of the vacuum box 1 and turn on the vacuum pump, vacuumize through the exhaust pipe 5, and maintain the vacuum degree of the vacuum box 1 to -0.085MPa;
[0061] 2) Ammonia fumigation and heat treatment: through the injection pipe 6 into the liquid reservoir 4 below the vacuum box 1 at a rate of 0.5kg / m 3 Liquid ammonia is injected into the fiberboard, and at the same time, the heating switch of the vacuum box 1 is turned on, and the medium and high density fiberboard is heat-treated at 60°C for 60 minutes. Then, the ...
Embodiment 2
[0065] A process for reducing aldehydes of medium and high density fiberboards, comprising the following steps:
[0066] 1) Vacuum sealing: Place 100 sheets of medium and high-density fiberboards with a density of 0.85g / cm³ and an initial formaldehyde content of 14mg / 100g evenly on the display rack 2, with an interval of 15mm between each fiberboard, and then carry them through the track 3 Push the trolley of the display rack 2 into the vacuum box 1, close the door of the vacuum box 1 and turn on the vacuum pump, vacuumize through the exhaust pipe 5, and maintain the vacuum degree of the vacuum box 1 to -0.088MPa;
[0067] 2) Ammonia fumigation and heat treatment: through the injection pipe 6 into the liquid reservoir 4 below the vacuum box 1 at a rate of 0.8kg / m 3 Liquid ammonia is injected into the fiberboard, and at the same time, the heating switch of the vacuum box 1 is turned on, and the medium and high density fiberboard is heat-treated at 60°C for 30 minutes. Then, the...
Embodiment 3
[0071] A process for reducing aldehydes of medium and high density fiberboards, comprising the following steps:
[0072] 1) Vacuum sealing: Place 50 sheets of medium and high-density fiberboards with a density of 0.83g / cm³ and an initial formaldehyde content of 16.5mg / 100g evenly on the display rack 2, with an interval of 15mm between each fiberboard, and then carry them through the track 3 Push the trolley of the display rack 2 into the vacuum box 1, close the door of the vacuum box 1 and turn on the vacuum pump, vacuumize through the exhaust pipe 5, and maintain the vacuum degree of the vacuum box 1 to -0.090MPa;
[0073] 2) Ammonia fumigation and heat treatment: through the injection pipe 6 into the liquid reservoir 4 below the vacuum box 1 at a rate of 0.6kg / m 3 Liquid ammonia is injected into the fiberboard, and at the same time, the heating switch of the vacuum box 1 is turned on, and the medium and high density fiberboard is heat-treated at 70°C for 40 minutes. Then, th...
PUM
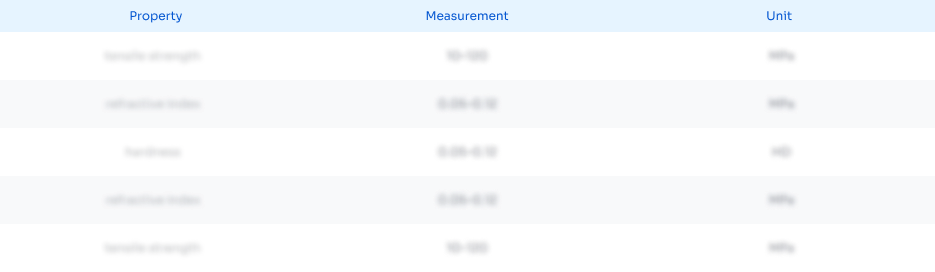
Abstract
Description
Claims
Application Information

- Generate Ideas
- Intellectual Property
- Life Sciences
- Materials
- Tech Scout
- Unparalleled Data Quality
- Higher Quality Content
- 60% Fewer Hallucinations
Browse by: Latest US Patents, China's latest patents, Technical Efficacy Thesaurus, Application Domain, Technology Topic, Popular Technical Reports.
© 2025 PatSnap. All rights reserved.Legal|Privacy policy|Modern Slavery Act Transparency Statement|Sitemap|About US| Contact US: help@patsnap.com