Control device for compensation of elastic deformation of articulated robot
A multi-joint robot, elastic deformation technology, applied in the direction of robot, computer control, control using feedback, etc., can solve the problems of poor trajectory accuracy, poor accuracy, and difficulty in consistency.
- Summary
- Abstract
- Description
- Claims
- Application Information
AI Technical Summary
Problems solved by technology
Method used
Image
Examples
no. 1 Embodiment approach
[0095] By using the above-described elastic deformation compensation control device 10 , in the articulated robot 1 , the influence of the elastic deformation of each axis can be compensated, and motions such as swinging can be performed with high trajectory accuracy. However, the inventors of the present application have found that if the settings are not properly designed Figure 13 The dynamic characteristic (1) of the elastic deformation compensation control device 10 shown in the block diagram of d (1), that is, the first dynamic characteristic calculation unit 300 performs elastic deformation compensation and feedforward control, and vibration occurs at the tip of the welding torch. This situation is the same even if the first dynamic characteristic calculation unit 300 is disposed on the input side of the axial force torque calculation unit 200 . In addition, even if the first dynamic characteristic calculating part 300 is divided into two dynamic characteristic parts a...
no. 2 Embodiment approach
[0115] In addition, the waveform of the M-order filter used by the filter unit 302 may be a waveform in which the M-1 order differential value is continuous with respect to the waveform at the time of the step response of the M-order filter. On the other hand, the waveform of the M-order filter used by the filter unit 302 may be a waveform in which the M-2 order differential value is continuous with respect to the waveform at the time of the impulse response of the M-order filter.
[0116] That is, in the above-mentioned first embodiment, the M-order filter (equation (1)) that can be represented by a continuous-time transfer function was shown, but by performing impulse response approximation, the M-order filter can be approximated is the moving average filter. In addition, when expressing the M-order filter in fractional form, the order difference between the denominator and the numerator is M, and it is continuous up to the M-1 order differential value of the step response, ...
no. 3 Embodiment approach
[0127] Regarding the elastic deformation compensation control device 10 described in the first embodiment (refer to Figure 13 ), the inventors of the present application further conducted intensive research and found the following.
[0128] That is, in Figure 13 In the elastic deformation compensation control device 10 shown, if Gda=0, even the interpolation unit 301 composed of N-order curve interpolation where N+M is 3 or more and the filter unit composed of an M-order filter 302 to constitute the first dynamic characteristic calculation unit 300, and the vibration of the tip of the welding torch can also be reliably suppressed. Furthermore, the influence of the elastic deformation of each axis can be compensated, and motions such as swinging can be performed with high trajectory accuracy.
[0129] In particular, the inventors of the present application have also found that if Gda=Gdv=0, the interpolation unit 301 composed of N-order curve interpolation where N+M is 2 or...
PUM
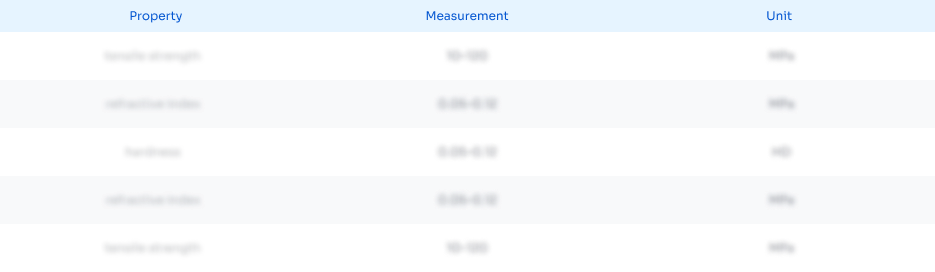
Abstract
Description
Claims
Application Information

- Generate Ideas
- Intellectual Property
- Life Sciences
- Materials
- Tech Scout
- Unparalleled Data Quality
- Higher Quality Content
- 60% Fewer Hallucinations
Browse by: Latest US Patents, China's latest patents, Technical Efficacy Thesaurus, Application Domain, Technology Topic, Popular Technical Reports.
© 2025 PatSnap. All rights reserved.Legal|Privacy policy|Modern Slavery Act Transparency Statement|Sitemap|About US| Contact US: help@patsnap.com