Chemical machinery planarization process method
A chemical-mechanical and process method technology, applied in the field of chemical-mechanical planarization, can solve problems such as circuit failure yield rate, influence device performance, and reduction, and achieve the effects of reducing metal loss and improving performance and yield.
- Summary
- Abstract
- Description
- Claims
- Application Information
AI Technical Summary
Problems solved by technology
Method used
Image
Examples
Embodiment Construction
[0021] Embodiments of the present invention are described in detail below, examples of which are shown in the drawings, wherein the same or similar reference numerals designate the same or similar elements or elements having the same or similar functions throughout. The embodiments described below by referring to the figures are exemplary only for explaining the present invention and should not be construed as limiting the present invention.
[0022] In the present invention, in the planarization process of the ALD metal tungsten, the problem that the removal rate is too high causes great loss of other layers. For this, as figure 1 Shown, the present invention proposes following technical scheme:
[0023] Metal tungsten is filled by atomic layer deposition;
[0024] A first removal process and a second removal process are performed to achieve chemical mechanical planarization of metal tungsten, wherein the pressure and rotation speed in the second removal process are respect...
PUM
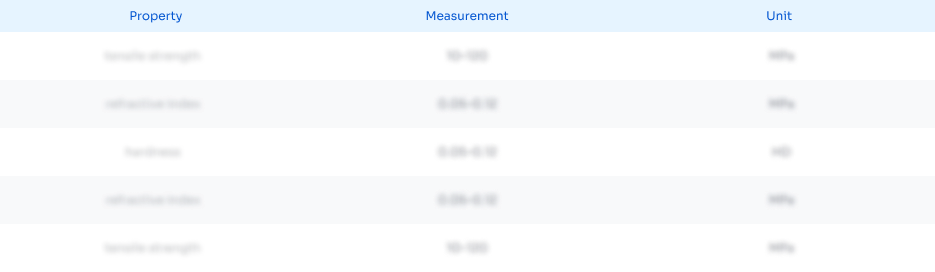
Abstract
Description
Claims
Application Information

- R&D
- Intellectual Property
- Life Sciences
- Materials
- Tech Scout
- Unparalleled Data Quality
- Higher Quality Content
- 60% Fewer Hallucinations
Browse by: Latest US Patents, China's latest patents, Technical Efficacy Thesaurus, Application Domain, Technology Topic, Popular Technical Reports.
© 2025 PatSnap. All rights reserved.Legal|Privacy policy|Modern Slavery Act Transparency Statement|Sitemap|About US| Contact US: help@patsnap.com