A thermal wind speed sensor structure and calibration method with zero point calibration function
A wind speed sensor, zero point calibration technology, applied in the testing/calibration of speed/acceleration/shock measurement equipment, instruments, speed/acceleration/shock measurement, etc. The cost of calibration and the effect of convenient packaging
- Summary
- Abstract
- Description
- Claims
- Application Information
AI Technical Summary
Problems solved by technology
Method used
Image
Examples
Embodiment Construction
[0013] The present invention will be further described below in conjunction with the accompanying drawings.
[0014] Such as figure 1 Shown is a thermal wind speed sensor structure with a zero point calibration function, including a circular ceramic substrate 1, a heating element 2 is arranged at the center of the back of the circular ceramic substrate 1, a first temperature measuring sensor 31 and a second measuring sensor The temperature sensors 32 are symmetrically distributed on the back of the circular ceramic substrate 1 with the heating element 2 as the center, and the first heating element 41 and the second heating element 42 are symmetrically distributed on the front of the circular ceramic substrate 1 with the heating element 2 as the center; The first heating element 41 is connected with the first lead pad 71 on the back side of the circular ceramic substrate 1 through the first wire 51 and the first through hole 61, and the second heating element 42 is connected wi...
PUM
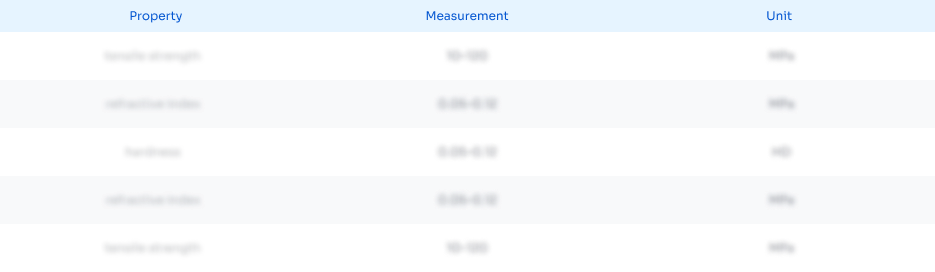
Abstract
Description
Claims
Application Information

- R&D
- Intellectual Property
- Life Sciences
- Materials
- Tech Scout
- Unparalleled Data Quality
- Higher Quality Content
- 60% Fewer Hallucinations
Browse by: Latest US Patents, China's latest patents, Technical Efficacy Thesaurus, Application Domain, Technology Topic, Popular Technical Reports.
© 2025 PatSnap. All rights reserved.Legal|Privacy policy|Modern Slavery Act Transparency Statement|Sitemap|About US| Contact US: help@patsnap.com