Space deployment mechanism driven based on multi-piezoelectric vibrator step crawling mode
A mode-driven, space-expanding technology, applied in generators/motors, piezoelectric effect/electrostrictive or magnetostrictive motors, electrical components, etc., can solve problems such as electromagnetic interference, complex structure, complex self-locking, etc. Achieve the effect of small weight, no electromagnetic interference, power-off self-locking energy consumption
- Summary
- Abstract
- Description
- Claims
- Application Information
AI Technical Summary
Problems solved by technology
Method used
Image
Examples
specific Embodiment approach 1
[0013] Specific implementation mode 1. Combination figure 1 and figure 2 Describe this specific embodiment. The space expansion mechanism driven by the multi-piezoelectric vibrator stepping and creeping mode described in this specific embodiment includes a base 1, two shaft sleeves, two expansion mechanisms 3, and four piezoelectric vibrators 4. , two drive shafts 5 and mounting base 2, through holes are opened at the center of the two opposite side walls of the base 1, and the through holes on the two side walls are coaxial, and the two shaft sleeves fixed in the two through holes, the two deployment mechanisms 3 are respectively fixed on the two opposite side walls of the base 1, the ends of the four piezoelectric vibrators 4 are all fixed inside the base 1 through the mounting base 2, and the four The head ends of the two piezoelectric vibrators 4 are located on the same straight line, one end of the two drive shafts 5 is closely connected with the two piezoelectric vibra...
specific Embodiment approach 2
[0016] Specific embodiment two, combine figure 1 and figure 2 This specific embodiment is described. The difference between this specific embodiment and the space expansion mechanism driven by the multi-piezoelectric vibrator stepping and creeping mode described in the first specific embodiment is that the mounting seat 2 and the base 1 are fixedly connected by bolts 6 .
specific Embodiment approach 3
[0017] Specific embodiment three, combine Figure 1-Figure 3 This specific embodiment is described. The difference between this specific embodiment and the space expansion mechanism driven by the multi-piezoelectric vibrator stepping creep mode described in the first specific embodiment is that each piezoelectric vibrator 4 includes a metal base 4-2, A plurality of piezoelectric ceramic sheets 4-3, a horn 4-4 and a driving foot 4-1, the plurality of piezoelectric ceramic sheets 4-3 are sequentially stacked between the metal base 4-2 and the horn 4-4 Between, the side of the metal base 4-2 is fixedly connected with the mounting seat 2, the horn 4-4 is a block body whose cross-section gradually becomes thinner, and the large end of the horn 4-4 is connected to the piezoelectric ceramic sheet 4-3 , The small end of the horn 4-4 is provided with a driving foot 4-1, and the side of the driving foot 4-1 is connected with the outer surface of the driving shaft 5.
PUM
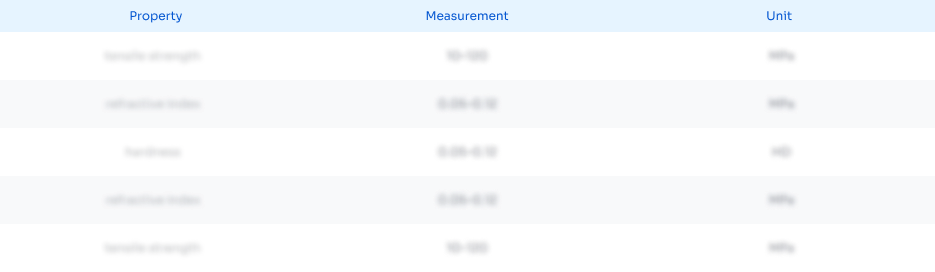
Abstract
Description
Claims
Application Information

- Generate Ideas
- Intellectual Property
- Life Sciences
- Materials
- Tech Scout
- Unparalleled Data Quality
- Higher Quality Content
- 60% Fewer Hallucinations
Browse by: Latest US Patents, China's latest patents, Technical Efficacy Thesaurus, Application Domain, Technology Topic, Popular Technical Reports.
© 2025 PatSnap. All rights reserved.Legal|Privacy policy|Modern Slavery Act Transparency Statement|Sitemap|About US| Contact US: help@patsnap.com