Insulation extruding and winding production line for twisted electric wires
A twisted wire and production line technology, applied in the direction of conductor/cable insulation, circuits, electrical components, etc., can solve the problems of uneven insulation, uneven center distribution, and fewer wires, so as to achieve easy collection and storage, Good insulation effect and long service life
- Summary
- Abstract
- Description
- Claims
- Application Information
AI Technical Summary
Problems solved by technology
Method used
Image
Examples
Embodiment 1
[0043]Embodiment 1: A stranded wire insulation extrusion and winding production line, which sequentially includes a stranded wire stretching device 1, a wire insulation skin processing equipment 2 and a wire stretching and winding device 3, and the wire insulation skin processing equipment 2 includes Stranded wire inlet 21, insulated wire outlet 22, the molding section 23 that connects described twisted wire inlet 21 and insulated wire outlet 22, the extruding section 24 that is connected with molding section 23, and to output from the insulated wire outlet 22 The shaping section 25 that the insulated wire plays a role in cooling and shaping; it also includes a wire insulation skin stretching device 26; the forming section 23 is provided with a first heating portion 231, and the extruding section 24 is provided with a second heating portion 241. There are two second heating parts 241 , which are respectively located on two sides of the extruding section 24 .
[0044] The wire ...
Embodiment 2
[0045] Embodiment 2: A stranded wire insulation extrusion and winding production line, which sequentially includes a stranded wire stretching device 1, a wire insulation skin processing equipment 2 and a wire stretching and winding device 3, and the wire insulation skin processing equipment 2 includes Stranded wire inlet 21, insulated wire outlet 22, the molding section 23 that connects described twisted wire inlet 21 and insulated wire outlet 22, the extruding section 24 that is connected with molding section 23, and to output from the insulated wire outlet 22 The shaping section 25 that the insulated wire plays a role in cooling and shaping; it also includes a wire insulation skin stretching device 26; the forming section 23 is provided with a first heating portion 231, and the extruding section 24 is provided with a second heating portion 241. There are two second heating parts 241 , which are respectively located on two sides of the extruding section 24 .
[0046] Describe...
Embodiment 3
[0047] Embodiment 3: A stranded wire insulation extrusion and winding production line, which sequentially includes a stranded wire stretching device 1, a wire insulation skin processing equipment 2 and a wire stretching and winding device 3, and the wire insulation skin processing equipment 2 includes Stranded wire inlet 21, insulated wire outlet 22, the molding section 23 that connects described twisted wire inlet 21 and insulated wire outlet 22, the extruding section 24 that is connected with molding section 23, and to output from the insulated wire outlet 22 The shaping section 25 that the insulated wire plays a role in cooling and shaping; it also includes a wire insulation skin stretching device 26; the forming section 23 is provided with a first heating portion 231, and the extruding section 24 is provided with a second heating portion 241. There are two second heating parts 241 , which are respectively located on two sides of the extruding section 24 .
[0048] The wire...
PUM
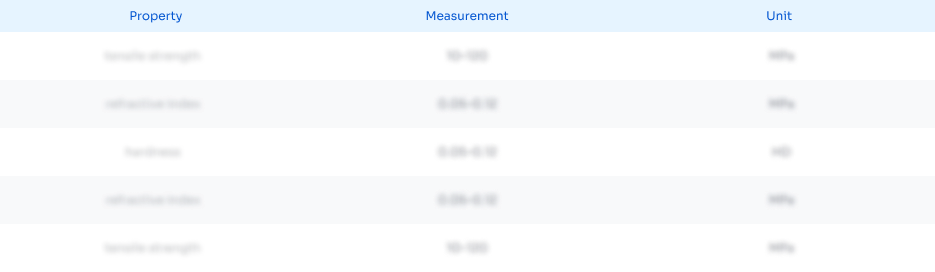
Abstract
Description
Claims
Application Information

- Generate Ideas
- Intellectual Property
- Life Sciences
- Materials
- Tech Scout
- Unparalleled Data Quality
- Higher Quality Content
- 60% Fewer Hallucinations
Browse by: Latest US Patents, China's latest patents, Technical Efficacy Thesaurus, Application Domain, Technology Topic, Popular Technical Reports.
© 2025 PatSnap. All rights reserved.Legal|Privacy policy|Modern Slavery Act Transparency Statement|Sitemap|About US| Contact US: help@patsnap.com