Asymmetric backfilling type friction stir spot welding method eliminating holes and annular trenches
A friction stir, asymmetric technology, used in non-electric welding equipment, welding equipment, metal processing equipment, etc., can solve the problems of unable to fill the gap of the stirring sleeve, insufficient plastic metal volume, root holes and surface ring groove defects, etc. Achieve the effect of eliminating holes and surface ring groove defects, compensating for metal volume loss, and eliminating surface ring groove defects
- Summary
- Abstract
- Description
- Claims
- Application Information
AI Technical Summary
Problems solved by technology
Method used
Image
Examples
specific Embodiment approach 1
[0020] Specific implementation mode one: combine Figure 1 to Figure 5 Describe this implementation mode, this implementation mode is realized through the following steps:
[0021] Step 1. Set the initial position of the welding tool: put the lower surface of the compression ring 1 in close contact with the upper surface of the plate to be welded 4, and adjust the lower surface of the stirring sleeve 2 and the lower surface of the stirring pin 3 to the compression ring 1. The lower surface is at the same level A, and this level A is set as the zero point of the spot welding process, at the same time, the stirring sleeve 2 and the stirring needle 3 start to rotate; see figure 1 ,
[0022] Step 2. Stirring sleeve 2 pricks down, stirring needle 3 withdraws: Stirring sleeve 2 at speed V 1 Penetrate down into the plate to be welded 4 until it reaches the predetermined penetration depth P, at the same time the stirring needle 3 2 Draw back upwards, so that the volume of the plas...
specific Embodiment approach 2
[0024] Specific implementation mode two: combination figure 2 Describe this embodiment, and this embodiment is the piercing velocity V of stirring sleeve 2 in the step 2 1 0.5mm / s. This lowering speed can make the plastic metal obtain better fluidity. Other components and connections are the same as those in the first embodiment.
specific Embodiment approach 3
[0025] Specific implementation mode three: combination figure 2 Describe this embodiment, and this embodiment is the piercing velocity V of stirring sleeve 2 in the step 2 1 is 1mm / s. This lowering speed can make the plastic metal obtain better fluidity. Other components and connections are the same as those in the first embodiment.
PUM
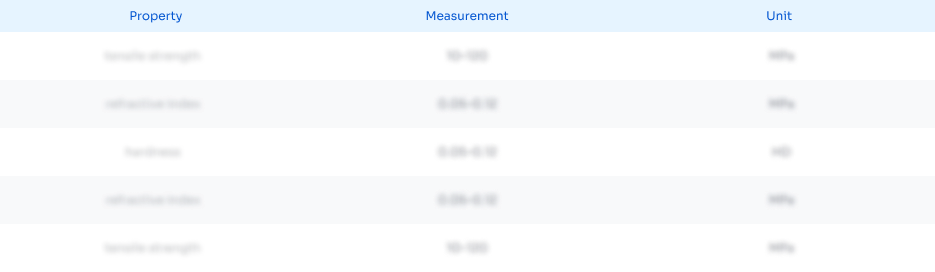
Abstract
Description
Claims
Application Information

- Generate Ideas
- Intellectual Property
- Life Sciences
- Materials
- Tech Scout
- Unparalleled Data Quality
- Higher Quality Content
- 60% Fewer Hallucinations
Browse by: Latest US Patents, China's latest patents, Technical Efficacy Thesaurus, Application Domain, Technology Topic, Popular Technical Reports.
© 2025 PatSnap. All rights reserved.Legal|Privacy policy|Modern Slavery Act Transparency Statement|Sitemap|About US| Contact US: help@patsnap.com