Method and depositing furnace for rapidly depositing and preparing C/C composite material by direct heating method
A composite material and deposition furnace technology, which is applied in the field of C/C composite material preparation, can solve the problems of long preparation cycle, high cost, and cost reduction, and achieve the effects of short preparation cycle, low cost and high safety.
- Summary
- Abstract
- Description
- Claims
- Application Information
AI Technical Summary
Problems solved by technology
Method used
Image
Examples
Embodiment 1
[0037] The processed prefabricated body (take the polyacrylonitrile-based carbon felt type as an example, the density is m=0.25g / cm 3, the size of the carbon felt is 200×10×5mm), electrification along the length direction, when the surface temperature of the preform reaches 700°C, the carbon source gas is introduced, with acetylene as the carbon source gas and nitrogen as the carrier gas, C 2 h 2 =10mL / min, N 2 =100mL / min, purify furnace N before reaction 2 The flow rate is 200mL / min, the purification is 15min, and the initial deposition current is 20A (the selection of the current value is related to the volume and density of the carbon felt, and the initial power per unit volume is 5*10 9 W·m -3 or so, select the appropriate current value), electrify in a steady flow state, deposit for 60h, the SEM appearance of the pyrolytic carbon deposited on the surface of the carbon felt is as follows figure 2 As shown, as the deposition progresses, the current remains constant und...
Embodiment 2
[0039] The processed prefabricated body (take the polyacrylonitrile-based carbon felt type as an example, the density is m=0.25g / cm 3 , cutting the carbon felt size is 200×10×5mm), electrifying along the length direction, when the surface temperature of the prefabricated body reaches 900°C, the carbon source gas is introduced, with acetylene as the carbon source gas and nitrogen as the carrier gas, C 2 h 2 =10mL / min, N 2 =200mL / min, purify furnace N before reaction 2 The flow rate is 200mL / min, the purification is 15min, and the initial deposition current is 20A (the selection of the current value is related to the volume and density of the carbon felt, and the initial power per unit volume is 5*10 9 W·m -3 left and right, select the appropriate current value), electrify in a steady flow state, and deposit for 60h. Finally, the densified material is graphitized to produce a C / C composite material.
Embodiment 3
[0041] Treated prefabricated body (take the polyacrylonitrile-based carbon felt type as an example, the density is m=0.25g / cm 3 , the size of the carbon felt is 200×10×5mm), electrification along the length direction, when the surface temperature of the preform reaches 1000°C, the carbon source gas is introduced, with methane as the carbon source gas, nitrogen as the carrier gas, CH 4 =10mL / min, N 2 =200mL / min, purify furnace N before reaction 2 The flow rate is 200mL / min, the purification is 15min, and the initial deposition current is 20A (the selection of the current value is related to the volume and density of the carbon felt, and the initial power per unit volume is 5*10 9 W·m -3 left and right, select the appropriate current value), electrify in a steady flow state, and deposit for 60h. Finally, the densified material is graphitized to produce a C / C composite material.
PUM
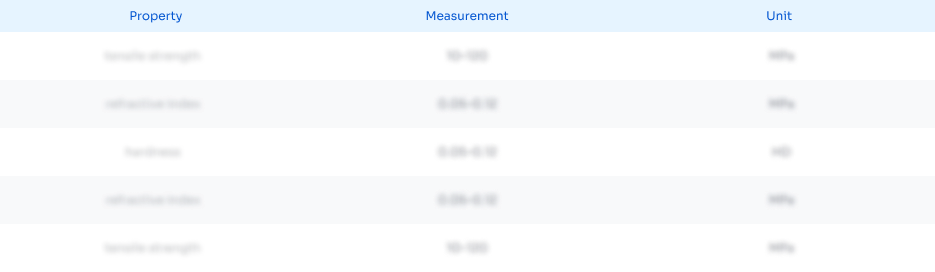
Abstract
Description
Claims
Application Information

- Generate Ideas
- Intellectual Property
- Life Sciences
- Materials
- Tech Scout
- Unparalleled Data Quality
- Higher Quality Content
- 60% Fewer Hallucinations
Browse by: Latest US Patents, China's latest patents, Technical Efficacy Thesaurus, Application Domain, Technology Topic, Popular Technical Reports.
© 2025 PatSnap. All rights reserved.Legal|Privacy policy|Modern Slavery Act Transparency Statement|Sitemap|About US| Contact US: help@patsnap.com