Control method and system for wet method leather manufacturing
A drying system and wet process technology, applied in drying solid materials, drying gas arrangement, drying and other directions, can solve the problems of low heat recovery rate of heat transfer oil, unsatisfactory drying, poor surface quality, etc., to improve the surface quality, Good production demand, timely control effect
- Summary
- Abstract
- Description
- Claims
- Application Information
AI Technical Summary
Problems solved by technology
Method used
Image
Examples
Embodiment Construction
[0028] The invention will be further described below in conjunction with the accompanying drawings.
[0029] see figure 1 , a wet-process tanning drying system includes a high-temperature heat exchanger 1, a medium-temperature heat exchanger 2, and a drying cylinder group 3, and the drying cylinder group 3 includes a plurality of drying cylinders 22, and the high-temperature heat exchanger 1 and the medium-temperature heat exchanger 2 tubes One end of the valve is connected to the steam pipe through the high temperature valve 11 and the medium temperature valve 12 respectively, and the other end is respectively connected to the first flash tank 4 and the second flash tank 5, and one end of the shell side of the high temperature heat exchanger 1 and the medium temperature heat exchanger 2 is connected Connect the cold air pipe, the other end is connected to the hot air pipe, the steam outlet of the first flash tank 4 is connected to the medium temperature heat exchanger 2, the ...
PUM
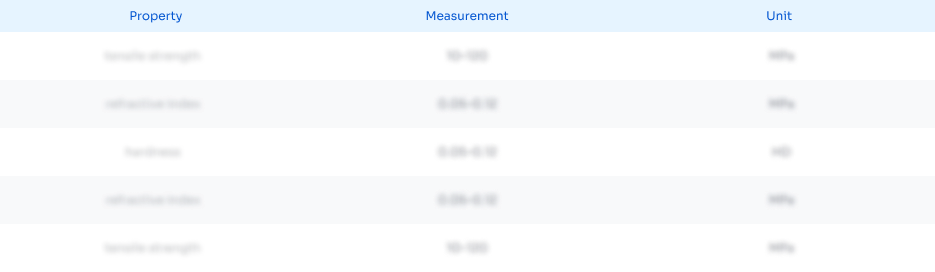
Abstract
Description
Claims
Application Information

- R&D
- Intellectual Property
- Life Sciences
- Materials
- Tech Scout
- Unparalleled Data Quality
- Higher Quality Content
- 60% Fewer Hallucinations
Browse by: Latest US Patents, China's latest patents, Technical Efficacy Thesaurus, Application Domain, Technology Topic, Popular Technical Reports.
© 2025 PatSnap. All rights reserved.Legal|Privacy policy|Modern Slavery Act Transparency Statement|Sitemap|About US| Contact US: help@patsnap.com