Optical fiber surface coating adhesive preparation method
A technology of surface coating and optical fiber, applied in the direction of coating, etc., can solve the problems of affecting the transmission performance of optical fiber and not having heat insulation effect, and achieve the effect of protecting optical fiber, excellent thermal stability, and improving high temperature resistance and low temperature resistance
- Summary
- Abstract
- Description
- Claims
- Application Information
AI Technical Summary
Problems solved by technology
Method used
Examples
Embodiment 1
[0019] A preparation method for optical fiber surface coating glue, it comprises the following steps:
[0020] S1. Kneading: In the rubber kneader, add high molecular weight polyisobutylene, silicone rubber, medium molecular weight polyisobutylene, low molecular weight polyisobutylene, antioxidant, glass fiber, and silicate for kneading. The kneading time is 30 to 50 minutes. The temperature is 120-160°C, calculated in parts by weight, silicone rubber: 25-30 parts; high-molecular-weight polyisobutene: 5-10 parts; medium-molecular-weight polyisobutene: 5-10 parts; low-molecular-weight polyisobutene: 10-15 parts parts; antioxidant: 0.5-1 part; glass fiber: 5-10 parts; silicate: 5-10 parts;
[0021] S2. Blending: After the kneading is completed, add inorganic fillers for blending. The blending time is 30-50 minutes, the temperature is 120-160°C, and the blending speed is 200-280rpm. Calculated by weight, inorganic fillers: 10-15 share;
[0022] S3. Extrusion: Extrude the blende...
PUM
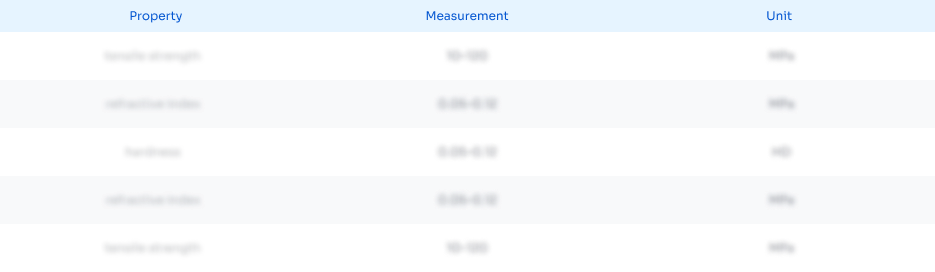
Abstract
Description
Claims
Application Information

- R&D
- Intellectual Property
- Life Sciences
- Materials
- Tech Scout
- Unparalleled Data Quality
- Higher Quality Content
- 60% Fewer Hallucinations
Browse by: Latest US Patents, China's latest patents, Technical Efficacy Thesaurus, Application Domain, Technology Topic, Popular Technical Reports.
© 2025 PatSnap. All rights reserved.Legal|Privacy policy|Modern Slavery Act Transparency Statement|Sitemap|About US| Contact US: help@patsnap.com