Chipping and breaking device
A crushing device and chip technology, which is applied in the field of chip crushing devices for aluminum alloy chips, can solve the problems that there is no aluminum alloy chip briquetting and recycling, chips cannot enter the compression chamber smoothly, and active and effective feeding cannot be formed.
- Summary
- Abstract
- Description
- Claims
- Application Information
AI Technical Summary
Problems solved by technology
Method used
Image
Examples
Embodiment 1
[0016] Such as figure 1 , 2 , 3, 4, and 5, the chip crushing device of this embodiment includes a chip receiving basket 10, a chip device 20, and a discharge device 30. The chip receiving basket 10 is set in a square funnel shape, and the throat is connected to the chip Device 20, the chip cutting device 20 includes a crushing roller 21, a crushing roller reducer 22 for driving the crushing roller 21 to rotate, and a knife-edge plate 23, and the crushing roller 21 is processed with several cutter heads evenly spaced longitudinally, each knife There are 4 cutter heads evenly distributed on the disc, and the knives of two adjacent cutter discs are misaligned with each other. The knife edge plate 23 is installed in parallel with the crushing roller 21, and the edge of the cutter head on the crushing roller 21 and the knife edge plate 23 The gap between the cutting edges is 1 to 3 mm. The chip receiving basket 10 holds the aluminum alloy chips that need to be crushed. In the non...
Embodiment 2
[0018] Such as figure 2 , 4 , 5, 6 This embodiment improves the included angle of the cutting edge of the knife edge plate. The position of the knife edge plate 23 for chips is the edge of the knife edge plate, and the edge of the knife edge plate is set at an angle of 70°. The included angle is 70°, and the cutting edge of the cutter head and the cutting edge of the knife edge plate are set opposite to each other. This included angle can not only ensure that the cutting edge is not easily damaged by the cutting chips, but also ensure the sharpness of the cutting edge of the cutting edge and the cutting edge of the cutting edge plate when cutting chips.
Embodiment 3
[0020] Such as figure 2 , 4 As shown, in this embodiment, in order to smoothly send the chopped chips into the compression chamber, the discharge device 30 is improved. The discharge device 30 is composed of a chip feeding chamber 31, a screw feeding rod 32 installed below the chip feeding chamber 31, and a driving screw. The feed rod reducer 33 for the feed rod 32 to rotate and the discharge port 34 located at the tail end of the screw feed rod 32 are composed. The chip feed chamber 31 is arranged directly below the crushing roller 21 . After being chopped, the chips fall into the chip feeding chamber 31, and then fall on the screw feeding rod 32. The screw feeding rod 32 rotates under the action of the feeding rod reducer 33, and the chips are pressed into blocks and sent out from the discharge port 34. Enter the next process.
PUM
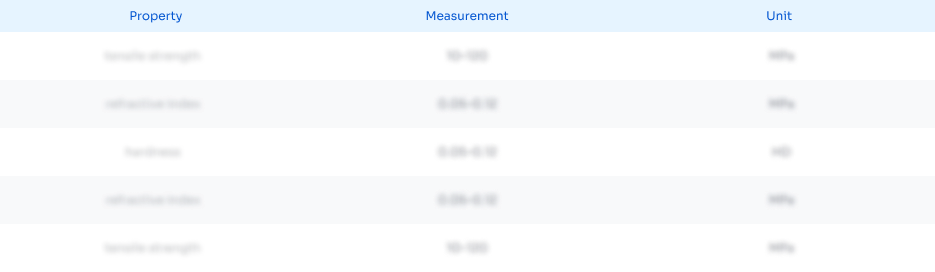
Abstract
Description
Claims
Application Information

- R&D
- Intellectual Property
- Life Sciences
- Materials
- Tech Scout
- Unparalleled Data Quality
- Higher Quality Content
- 60% Fewer Hallucinations
Browse by: Latest US Patents, China's latest patents, Technical Efficacy Thesaurus, Application Domain, Technology Topic, Popular Technical Reports.
© 2025 PatSnap. All rights reserved.Legal|Privacy policy|Modern Slavery Act Transparency Statement|Sitemap|About US| Contact US: help@patsnap.com