Chemical dry etching machine equipped with pumping pipeline pressure monitoring device
A chemical dry method and monitoring device technology, applied in electrical components, semiconductor/solid-state device manufacturing, circuits, etc., can solve the problems of APC component failure, isolation valve failure, dry pump efficiency attenuation, etc., and achieve the effect of eliminating failures
- Summary
- Abstract
- Description
- Claims
- Application Information
AI Technical Summary
Problems solved by technology
Method used
Image
Examples
Embodiment Construction
[0016] The present invention will be further elaborated below by describing a preferred specific embodiment in detail in conjunction with the accompanying drawings.
[0017] Such as figure 1 As shown, a chemical dry etching machine equipped with a pumping pipeline pressure monitoring device includes a process chamber 1 connected in sequence through a pumping pipeline 3, an isolation valve 4, an automatic pressure controller 5 and a dry pump 2; the automatic pressure control A commercially available digital pressure detector 6 is arranged between the device 5 and the dry pump 2; the digital pressure detector 6 is arranged outside the pumping pipeline 3; the digital pressure detector 6 is used to detect the pressure change of the pumping pipeline 3. A plurality of O-rings 31 are evenly distributed on the outside of the pumping pipeline 3 .
[0018] Specific application: When the process room encounters "exhaust cannot be completed within the set time", we can block the port bet...
PUM
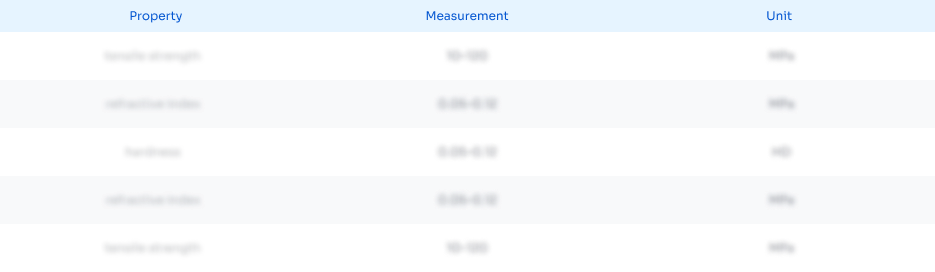
Abstract
Description
Claims
Application Information

- R&D
- Intellectual Property
- Life Sciences
- Materials
- Tech Scout
- Unparalleled Data Quality
- Higher Quality Content
- 60% Fewer Hallucinations
Browse by: Latest US Patents, China's latest patents, Technical Efficacy Thesaurus, Application Domain, Technology Topic, Popular Technical Reports.
© 2025 PatSnap. All rights reserved.Legal|Privacy policy|Modern Slavery Act Transparency Statement|Sitemap|About US| Contact US: help@patsnap.com