Dry-type capacitor type composite insulating sleeve pipe production method
A composite insulation and production method technology, applied in the direction of lead-in/through-type insulators, insulators, insulators, etc., can solve the problems of easy breakdown and partial discharge, and achieve the effect of avoiding breakdown and reducing the generation of micropores
- Summary
- Abstract
- Description
- Claims
- Application Information
AI Technical Summary
Problems solved by technology
Method used
Examples
Embodiment 1
[0023] The production method of the dry capacitor type composite insulating bushing of the present invention is realized through the following steps:
[0024] The first step, tape winding: take a metal tubular conductor, have a grease injection port and an exhaust port at both ends of the conductor, wrap several layers of glass fiber cloth tape and semiconductor conformable material on the surface of the conductor, and the glass fiber Interlaced winding of cloth tape and semi-conductive conformable material;
[0025] The second step, wrapping: put a heat-shrinkable sleeve on the outer wall of the conductor wrapped with cloth tape, and then vacuumize the space between the heat-shrinkable sleeve and the conductor, so that the heat-shrinkable sleeve is tightly attached to the on the outer wall of the conductor. In this embodiment, the model of the heat shrinkable sleeve is ZRRAXSLEEVESBI300 / 350.
[0026] The third step, grease injection: under the vacuum state of -90--100KPa, p...
Embodiment 2
[0031] The first step, tape winding: take a metal tubular conductor, have a grease injection port and an exhaust port at both ends of the conductor, wrap several layers of glass fiber cloth tape and semiconductor conformable material on the surface of the conductor, and the glass fiber Interlaced winding of cloth tape and semi-conductive conformable material;
[0032] The second step, wrapping: put a heat-shrinkable sleeve on the outer wall of the conductor wrapped with cloth tape, and then vacuumize the space between the heat-shrinkable sleeve and the conductor, so that the heat-shrinkable sleeve is tightly attached to the on the outer wall of the conductor. In this embodiment, the model of the heat shrinkable sleeve is ZRRAXSLEEVESBI300 / 350.
[0033] The third step, grease injection: under the vacuum state of -90--100KPa, pour epoxy resin into the cavity between the heat shrinkable sleeve and the conductor from the grease injection port on the conductor until the resin is f...
PUM
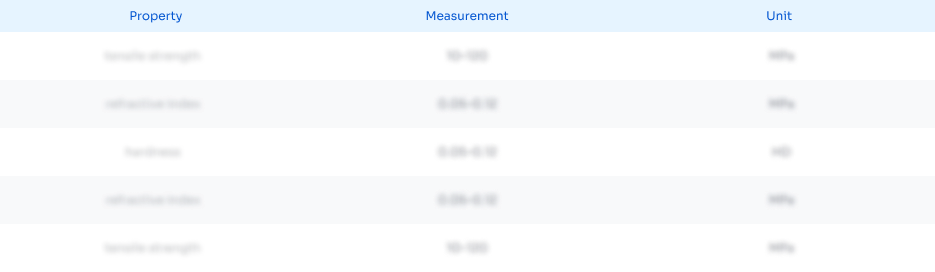
Abstract
Description
Claims
Application Information

- Generate Ideas
- Intellectual Property
- Life Sciences
- Materials
- Tech Scout
- Unparalleled Data Quality
- Higher Quality Content
- 60% Fewer Hallucinations
Browse by: Latest US Patents, China's latest patents, Technical Efficacy Thesaurus, Application Domain, Technology Topic, Popular Technical Reports.
© 2025 PatSnap. All rights reserved.Legal|Privacy policy|Modern Slavery Act Transparency Statement|Sitemap|About US| Contact US: help@patsnap.com