drilling system
A lifting system, hydraulic drilling rig technology, applied in boring/drilling, drilling/drilling equipment, components of boring machine/drilling machine, etc., can solve the problems of ununiform drilling quality, low production quality, low processing efficiency, etc. , to achieve the effect of improving drilling efficiency, improving stability, and the same feeding force
- Summary
- Abstract
- Description
- Claims
- Application Information
AI Technical Summary
Problems solved by technology
Method used
Image
Examples
Embodiment 1
[0022] Embodiment 1: as figure 1 , 2 As shown in .3, a drilling system includes a frame 01, a feeding system 03 and a lifting system 02 are arranged on the frame, an upper lifting frame 021 and a lower lifting frame 022 are connected to the lifting system, and the top of the upper lifting frame is set There are several hydraulic drilling rigs 04 arranged vertically. The driving shaft 041 of the hydraulic drilling rig is connected with the first coupling 05. The angle between the driving shaft of the hydraulic drilling rig and the telescopic shaft is 160°. The lower end of the first coupling is connected to There is a telescopic shaft, the lower end of the telescopic shaft is connected with a connecting shaft 08, the lower end of the connecting shaft is connected with a second coupling 09, the lower end of the second coupling is connected with a drill bit 10, and the outer sleeve of the drill bit is provided with a positioning sleeve 11, and the positioning sleeve Fixed on the...
Embodiment 2
[0024] Embodiment 2: The structure of this embodiment is basically the same as that of Embodiment 1, the difference is that, as Figure 9 As shown, there are five pulse gas charging holes 075 on the lower end surface of the fixed shaft. The pulse gas inlet holes are distributed in a circular arc. The radius length of the air intake cavity is the same. One end of the sliding shaft inside the fixed shaft is provided with a piston that matches the diameter of the air chamber. When the gas volume in the air chamber increases, the piston can be pushed to move, thereby realizing the relative movement between the sliding shaft and the fixed shaft, and elongating the telescopic shaft; When the amount of gas in the air chamber decreases, it can attract the movement of the piston, and then shrink the telescopic shaft. The outer sleeve of the connecting shaft is provided with an air intake sleeve, which is connected with the connecting shaft through a rotating bearing. When the connecti...
PUM
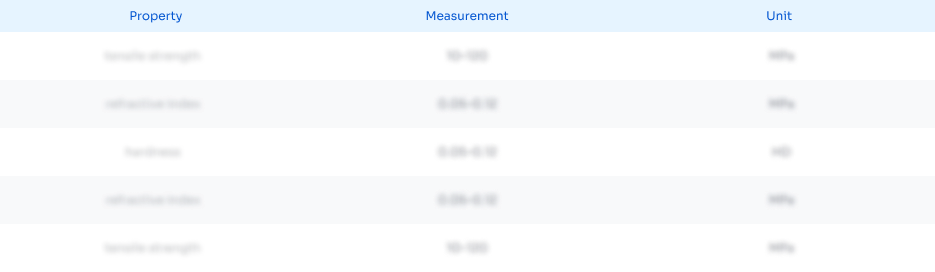
Abstract
Description
Claims
Application Information

- R&D
- Intellectual Property
- Life Sciences
- Materials
- Tech Scout
- Unparalleled Data Quality
- Higher Quality Content
- 60% Fewer Hallucinations
Browse by: Latest US Patents, China's latest patents, Technical Efficacy Thesaurus, Application Domain, Technology Topic, Popular Technical Reports.
© 2025 PatSnap. All rights reserved.Legal|Privacy policy|Modern Slavery Act Transparency Statement|Sitemap|About US| Contact US: help@patsnap.com