Quantitative filter paper and preparing method and application thereof
A quantitative filter paper, mass ratio technology, applied in filter paper, paper, papermaking and other directions, can solve the problems of filtration speed, filtration accuracy and stability need to be further unified, high production cost of quantitative filter paper, to achieve high stability, low cost, high performance stable effect
- Summary
- Abstract
- Description
- Claims
- Application Information
AI Technical Summary
Problems solved by technology
Method used
Image
Examples
Embodiment 1
[0022] 1. Put 20kg of cotton pulp with a beating degree of 16°SR on the sheet-making net to form, press, and dry to obtain the inflow layer;
[0023] 2. Put the inflow layer prepared in step 1 on the lamination net, cover the inflow layer with 20kg of cotton pulp with a beating degree of 20°SR, and then form, press, and dry to obtain the composite layer of the inflow layer-intermediate layer ;
[0024] 3. Put the composite layer of the inflow layer-intermediate layer prepared in step 2 on the lamination net, cover the interlayer with 10kg of cotton pulp with a beating degree of 24°SR, and then form, press, and dry to obtain the inflow layer - Composite layer of middle layer - outflow layer;
[0025] 4. The composite layer of the inflow layer-middle layer-outflow layer prepared in step 3 is impregnated with a mixed acid of hydrochloric acid and hydrofluoric acid with a concentration of 5wt% for 7 hours, then neutralized with alkali, and then washed with deionized water Multip...
Embodiment 2
[0028] 1. Put 30kg of kraft wood pulp with a beating degree of 17°SR on a sheet net for forming, pressing, and drying to obtain the inflow layer;
[0029] 2. Put the inflow layer prepared in step 1 on the sheet net, cover the inflow layer with 20 kg of kraft wood pulp with a beating degree of 21 ° SR, and then form, press, and dry to obtain the inflow layer-middle layer Composite layer;
[0030] 3, the composite layer of the inflow layer-middle layer prepared in step 2 is placed on the sheet net, and the kraft wood pulp of 25 ° SR is covered on the middle layer by 10kg beating degree, and then forming, pressing, drying, to obtain Composite layer of inflow layer-middle layer-outflow layer;
[0031] 4. The composite layer of the inflow layer-middle layer-outflow layer prepared in step 3 is impregnated with a mixed acid of hydrochloric acid and hydrofluoric acid with a concentration of 5.5wt% for 8 hours, then neutralized with alkali, and then deionized water Wash multiple time...
Embodiment 3
[0034] 1. Put 40kg of cotton pulp with a beating degree of 14°SR on the sheet-making net to form, press, and dry to obtain the inflow layer;
[0035] 2. Place the inflow layer prepared in step 1 on the lamination net, cover the inflow layer with 20kg of cotton pulp with a beating degree of 19°SR, and then form, press, and dry to obtain a composite layer of the inflow layer-intermediate layer ;
[0036] 3. Put the composite layer of the inflow layer-intermediate layer prepared in step 2 on the lamination net, cover the interlayer with 10kg of cotton pulp with a beating degree of 23°SR, and then form, press, and dry to obtain the inflow layer - Composite layer of middle layer - outflow layer;
[0037] 4. The composite layer of the inflow layer-middle layer-outflow layer prepared in step 3 is impregnated with a mixed acid of hydrochloric acid and hydrofluoric acid with a concentration of 4.5wt% for 6 hours, then neutralized with alkali, and then deionized water Wash multiple ti...
PUM
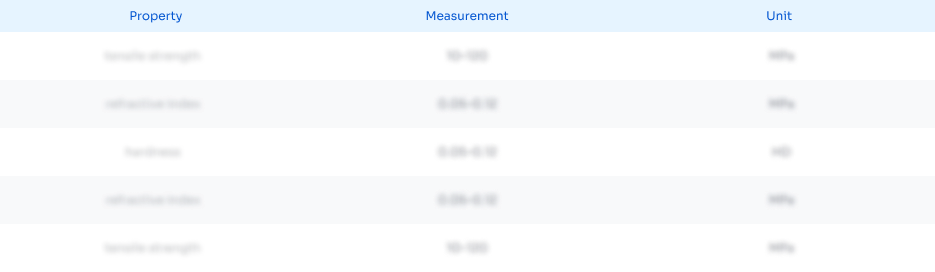
Abstract
Description
Claims
Application Information

- R&D Engineer
- R&D Manager
- IP Professional
- Industry Leading Data Capabilities
- Powerful AI technology
- Patent DNA Extraction
Browse by: Latest US Patents, China's latest patents, Technical Efficacy Thesaurus, Application Domain, Technology Topic, Popular Technical Reports.
© 2024 PatSnap. All rights reserved.Legal|Privacy policy|Modern Slavery Act Transparency Statement|Sitemap|About US| Contact US: help@patsnap.com