Robot hand-eye calibration method based on non-minimized and non-optimized algorithm
A technology of robot hand and calibration method, which is applied in the direction of manipulators and manufacturing tools, and can solve problems such as unsuitable hand-eye calibration and errors
- Summary
- Abstract
- Description
- Claims
- Application Information
AI Technical Summary
Problems solved by technology
Method used
Image
Examples
Embodiment Construction
[0091] The present invention will be further described below in conjunction with the accompanying drawings and embodiments.
[0092] A non-minimization optimization
[0093] system such as figure 1 As shown, the robot base is connected with the robot arm through the first rotation axis, and the robot arm includes the first section arm and the second section arm connected by the second rotation axis, the end of the second section arm is attached with an end effector, and the end execution A camera is fixed on the device. The robot moves through the arm, the end effector moves to the corresponding position, and the base remains fixed during the movement.
[0094] Such as figure 2 as shown,
[0095] 1. Determine the transformation matrix A from the camera to the world coordinate system i and the transformation matrix B from the base of the robot to the end effector i .
[0096] 1) Use the motion selection algorithm to select N motions of the robot end effector;
[0097] ...
PUM
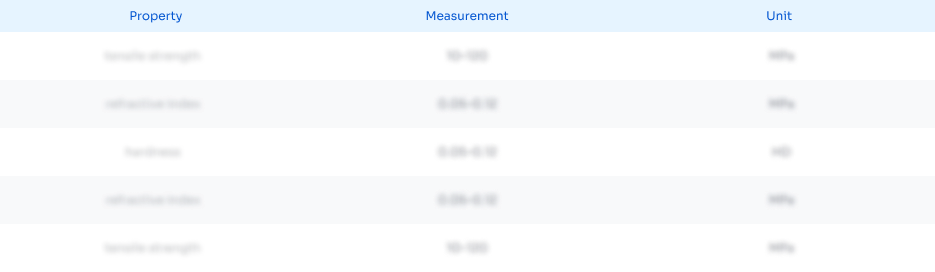
Abstract
Description
Claims
Application Information

- Generate Ideas
- Intellectual Property
- Life Sciences
- Materials
- Tech Scout
- Unparalleled Data Quality
- Higher Quality Content
- 60% Fewer Hallucinations
Browse by: Latest US Patents, China's latest patents, Technical Efficacy Thesaurus, Application Domain, Technology Topic, Popular Technical Reports.
© 2025 PatSnap. All rights reserved.Legal|Privacy policy|Modern Slavery Act Transparency Statement|Sitemap|About US| Contact US: help@patsnap.com