Concrete pipe pile production technology capable of recycling residual grout
A technology for concrete pipe piles and production processes, which is used in manufacturing tools, ceramic molding workshops, ceramic molding machines, etc., can solve problems such as large financial resources and manpower, secondary environmental pollution, etc., to prevent pollution, reduce costs, and solve environmental problems. Effect
- Summary
- Abstract
- Description
- Claims
- Application Information
AI Technical Summary
Problems solved by technology
Method used
Image
Examples
Embodiment 1
[0017] A production process for concrete pipe piles for recycling residual slurry, comprising the steps of batching, stirring, feeding, centrifugal forming, residual slurry collection, residual slurry treatment, residual slurry recovery and batching, and residual slurry treatment is to dilute the residual slurry and stir, the specific gravity of the diluted slurry is 1.41g / cm 3 .
[0018] The process of residual slurry collection, residual slurry treatment, residual slurry recovery and weighing batching is completed sequentially using the material collection tank, mixing tank, finished product tank, mixing building and water weighing hopper system.
[0019] The maximum interval time for the recycling of residual slurry is 1 hour when the temperature is 35°C.
[0020] When the production stops, flush the slurry water collection tank and mixing tank in time to ensure that there is no slurry water balance on the side wall.
[0021] When there is no slurry water in the mixing ta...
Embodiment 2
[0023] A production process for concrete pipe piles for recycling residual slurry, comprising the steps of batching, stirring, feeding, centrifugal forming, residual slurry collection, residual slurry treatment, residual slurry recovery and batching, and residual slurry treatment is to dilute the residual slurry and stir, the specific gravity of the diluted slurry is 1.40g / cm 3 .
[0024] The process of residual slurry collection, residual slurry treatment, residual slurry recovery and weighing batching is completed sequentially using the material collection tank, mixing tank, finished product tank, mixing building and water weighing hopper system.
[0025] The maximum interval for recycling the residual slurry is 1.5 hours when the temperature is 30°C.
[0026] When the production stops, flush the slurry water collection tank and mixing tank in time to ensure that there is no slurry water balance on the side wall.
[0027] When there is no slurry water in the mixing tank an...
Embodiment 3
[0029] A production process for concrete pipe piles for recycling residual slurry, comprising the steps of batching, stirring, feeding, centrifugal forming, residual slurry collection, residual slurry treatment, residual slurry recovery and batching, and residual slurry treatment is to dilute the residual slurry And stirring, the specific gravity of the diluted slurry is 1.39g / cm 3 .
[0030] The process of residual slurry collection, residual slurry treatment, residual slurry recovery and weighing batching is completed sequentially using the material collection tank, mixing tank, finished product tank, mixing building and water weighing hopper system.
[0031] The maximum interval time for the recycling of residual pulp is 1.8 hours when the temperature is <25°C.
[0032] When the production stops, flush the slurry water collection tank and mixing tank in time to ensure that there is no slurry water balance on the side wall.
[0033] When there is no slurry water in the mix...
PUM
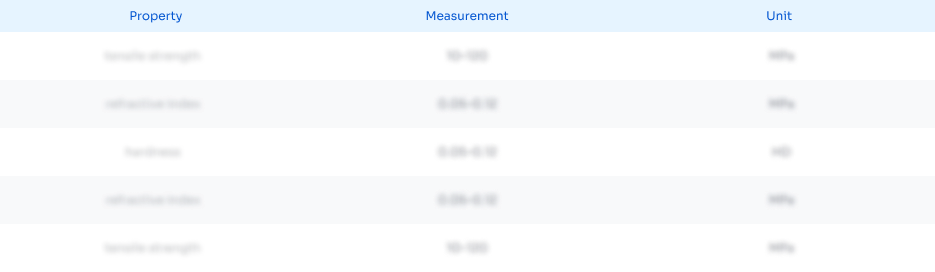
Abstract
Description
Claims
Application Information

- R&D Engineer
- R&D Manager
- IP Professional
- Industry Leading Data Capabilities
- Powerful AI technology
- Patent DNA Extraction
Browse by: Latest US Patents, China's latest patents, Technical Efficacy Thesaurus, Application Domain, Technology Topic, Popular Technical Reports.
© 2024 PatSnap. All rights reserved.Legal|Privacy policy|Modern Slavery Act Transparency Statement|Sitemap|About US| Contact US: help@patsnap.com