Pipeline robot vehicle with pitch varying spiral line type crawling ability
A robot car and helical technology, applied in the direction of special pipes, pipe components, mechanical equipment, etc., can solve the problems of difficult crawling, poor steering flexibility, etc., and achieve the effect of compact structure and high stability
- Summary
- Abstract
- Description
- Claims
- Application Information
AI Technical Summary
Problems solved by technology
Method used
Image
Examples
Embodiment Construction
[0042] The present invention will be further described below in conjunction with drawings and embodiments.
[0043] like figure 1 As shown, the pipeline locomotive of the present invention is a three-stage structure, comprising a front end motion mechanism 37, a rear end motion mechanism 35, a motion angle adjustment mechanism 36, a magnetic adsorption wheel 39 and an axial follower mechanism 38; the front end motion mechanism 37 and The rear end motion mechanism 35 has the same structure and is installed on the front section and the rear section of the pipeline locomotive respectively, and the motion angle adjustment mechanism 36 is installed on the middle section of the pipeline locomotive; the front end motion mechanism 37 is connected with the motion angle adjustment mechanism 36, and the motion angle adjustment mechanism 36 The axial follow-up mechanism 38 is axially connected with the rear-end motion mechanism 35, and the bottoms of the front-end motion mechanism 37 and ...
PUM
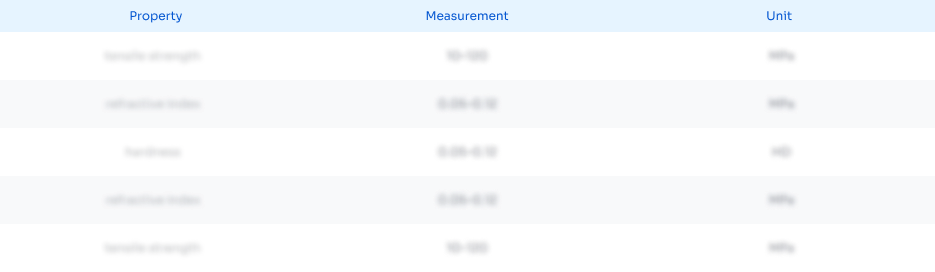
Abstract
Description
Claims
Application Information

- Generate Ideas
- Intellectual Property
- Life Sciences
- Materials
- Tech Scout
- Unparalleled Data Quality
- Higher Quality Content
- 60% Fewer Hallucinations
Browse by: Latest US Patents, China's latest patents, Technical Efficacy Thesaurus, Application Domain, Technology Topic, Popular Technical Reports.
© 2025 PatSnap. All rights reserved.Legal|Privacy policy|Modern Slavery Act Transparency Statement|Sitemap|About US| Contact US: help@patsnap.com