Coating for heat sublimation transfer printing and preparation method of coating
A thermal sublimation and transfer printing technology, applied in the direction of coating, etc., can solve the problems of high production cost, large dosage, slow drying speed, etc., and achieve the effects of saving direct production cost, reducing dosage and simple production
- Summary
- Abstract
- Description
- Claims
- Application Information
AI Technical Summary
Problems solved by technology
Method used
Examples
Embodiment 1
[0009] 1. The sublimation transfer coating includes the following components by weight: 90-115 parts of carboxymethyl cellulose sodium, 5-8 parts of inkjet medium adsorbent, 0.5-1.5 parts of defoamer, polyvinyl chloride 0.5-1.5 parts of resin, 800-1000 parts of water.
[0010] 2. The manufacturing method for the thermal sublimation transfer printing coating includes the following steps: A. Add 800-1000 kg of water into 90-115 kg of sodium carboxymethyl cellulose and stir evenly; B. Add 5-8kg of inkjet medium adsorbent to the methylcellulose sodium solution, and stir the mixture evenly; C. Add 0.5-1.5kg of polyvinyl chloride resin to the above-mentioned mixture, and stir evenly.
[0011] 3. The obtained thermal sublimation transfer coating was used in actual production. The test results showed that the drying speed of the ink absorption increased from the original average of 7 to 8 to 10 to 12 meters per hour, and the transfer rate increased from the existing coating to 10 to 1...
Embodiment 2
[0013] 1. The sublimation transfer coating includes the following components by weight: 90-115 parts of carboxymethyl cellulose sodium, 5-8 parts of inkjet medium adsorbent, 0.5-1.5 parts of defoamer, 0.5 parts of calcium carbonate ~1.5 parts, 800~1000 parts of water.
[0014] 2. The manufacturing method for sublimation transfer printing coating includes the following steps: A. Add 800-1000 kg of water into 90-115 kg of sodium carboxymethyl cellulose and stir evenly; B. Dilute carboxymethyl cellulose Add 5 to 8 kg of inkjet medium adsorbent to the cellulose-based sodium solution, and stir the mixture evenly; C, add 0.5 to 1.5 kg of calcium carbonate to the above mixture, and stir evenly.
[0015] 3. The obtained thermal sublimation transfer coating was used in actual production. The test results showed that the drying speed of the ink absorption increased from the original average of 7 to 8 to 10 to 12 meters per hour, and the transfer rate increased from the existing coating ...
PUM
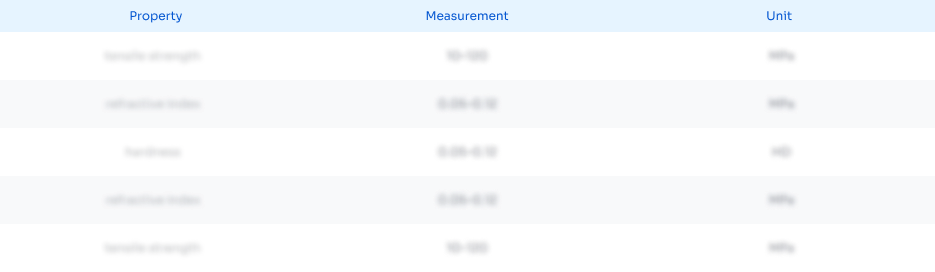
Abstract
Description
Claims
Application Information

- R&D
- Intellectual Property
- Life Sciences
- Materials
- Tech Scout
- Unparalleled Data Quality
- Higher Quality Content
- 60% Fewer Hallucinations
Browse by: Latest US Patents, China's latest patents, Technical Efficacy Thesaurus, Application Domain, Technology Topic, Popular Technical Reports.
© 2025 PatSnap. All rights reserved.Legal|Privacy policy|Modern Slavery Act Transparency Statement|Sitemap|About US| Contact US: help@patsnap.com