Method for recovering noble metal from waste titanium anodes with noble metal coatings
A precious metal and titanium anode technology, which is applied in the field of precious metal recovery, can solve the problems of increasing the difficulty of separating and purifying precious metals, affecting the surrounding environment, and long production cycle, and achieves the effects of shortening the separation and purification process cycle, reducing production costs, and reducing production costs.
- Summary
- Abstract
- Description
- Claims
- Application Information
AI Technical Summary
Problems solved by technology
Method used
Image
Examples
Embodiment 1
[0040] Raw material: 100kg waste titanium anode waste with precious metal coating, its main chemical composition: Ru 0.10%, Ir 0.16%, and the rest is Ti. The noble metal coating is a Ru-Ti-Ir ternary metal oxide coating;
[0041] Recycling steps:
[0042] (1) Put the following stripping agent in the reaction kettle: mix industrial grade sodium fluoride and magnesium chloride at a mass ratio of 1:5, add water to prepare a solution with a mass concentration of 80%; heat to 85°C, and The waste titanium anode with precious metal coating is immersed in the stripper in the reaction kettle, so that the waste titanium anode is completely immersed in the stripper, soaked for 20 minutes, so that the precious metal coating is stripped into the stripper; take out the remaining titanium anode, rinse with water Clean, then impregnate with a hydrofluoric acid solution with a mass concentration of 5%, and re-coat the remaining titanium anode with precious metal to obtain a new titanium anode...
Embodiment 2
[0048] Raw materials: 100kg of waste titanium anode waste with precious metal coating, its main chemical composition: Ru accounts for 0.10%, Ir accounts for 0.16%, and the rest is Ti. The waste precious metal coating is a Ru-Ti-Ir ternary metal oxide coating;
[0049] Recycling steps:
[0050] (1) Put the following stripping agent in the reaction kettle: mix industrial-grade potassium fluoride and calcium chloride at a mass ratio of 1:1, add water to prepare a solution with a mass concentration of 90%; heat to 95°C, and The waste titanium anode with precious metal coating to be treated is immersed in the stripper in the reaction kettle, so that the waste titanium anode is completely immersed in the stripper, soaked for 15 minutes, so that the precious metal coating is stripped into the stripper; take out the remaining titanium anode, After rinsing with water, soaking with a hydrochloric acid solution with a mass concentration of 17%, re-coating the remaining titanium anode wi...
Embodiment 3
[0056] Raw materials: 100kg of waste titanium anode waste with precious metal coating, its main chemical composition: Ru accounts for 0.10%, Ir accounts for 0.16%, and the rest is Ti. The waste precious metal coating is a Ru-Ti-Ir ternary metal oxide coating;
[0057] Recycling steps:
[0058] (1) Put the following stripping agents in the reaction kettle: mix industrial-grade calcium fluoride and sodium chloride at a mass ratio of 1:2, add water to prepare a solution with a mass concentration of 70%; heat to 100°C, and The waste titanium anode with precious metal coating to be treated is immersed in the stripper in the reactor, so that the waste titanium anode is completely immersed in the stripper, soaked for 16 minutes, so that the precious metal coating is stripped into the stripper; take out the remaining titanium anode, After rinsing with water, soaking with a hydrochloric acid solution with a mass concentration of 17%, re-coating the remaining titanium anode with precio...
PUM
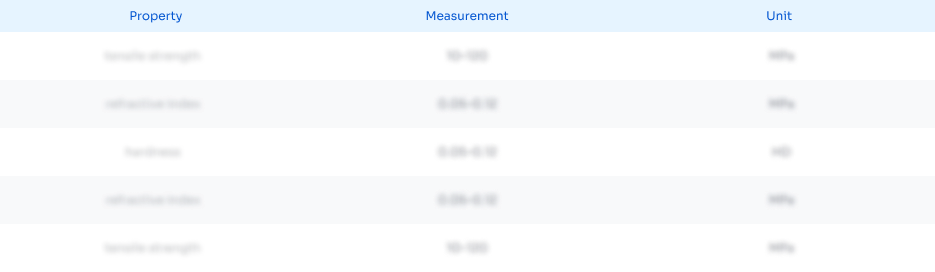
Abstract
Description
Claims
Application Information

- Generate Ideas
- Intellectual Property
- Life Sciences
- Materials
- Tech Scout
- Unparalleled Data Quality
- Higher Quality Content
- 60% Fewer Hallucinations
Browse by: Latest US Patents, China's latest patents, Technical Efficacy Thesaurus, Application Domain, Technology Topic, Popular Technical Reports.
© 2025 PatSnap. All rights reserved.Legal|Privacy policy|Modern Slavery Act Transparency Statement|Sitemap|About US| Contact US: help@patsnap.com