Hot-upset mold
A mold and hot upsetting technology, which is applied in the manufacture of tools, forging/pressing/hammer devices, forging/pressing/hammering machines, etc., can solve problems such as increased production costs, inability to guarantee process size requirements, and poor end precision. , to achieve the effect of saving time, simple structure and convenient operation
- Summary
- Abstract
- Description
- Claims
- Application Information
AI Technical Summary
Problems solved by technology
Method used
Image
Examples
Embodiment Construction
[0009] Such as figure 1 with figure 2 As shown, a hot upsetting mold includes an upper template 1 and a lower template 2. The upper template 1 and the lower template 2 are guided by a guide sleeve 3 and a guide column 4. The upper mold 5 is fixed on the upper template 1 by bolts. , the end of the upper die 5 is provided with a blind hole 6 for positioning the bar, which can contain the upper end of the bar to prevent deformation of the upper end of the bar during upsetting. A slideway 7 is fixed on the lower template 2, and the lower die 8 and The slideway 7 is guided and connected, and the lower mold 8 is provided with a cavity 9; the lower mold 8 is provided with a push-pull handle 10, and the lower template 2 is provided with a material return gap 11. The final workpiece can fall from the material return gap 11; the lower mold 8 and the lower template 2 form a closed cavity during work to ensure that the metal is completely filled according to the shape of the cavity, so ...
PUM
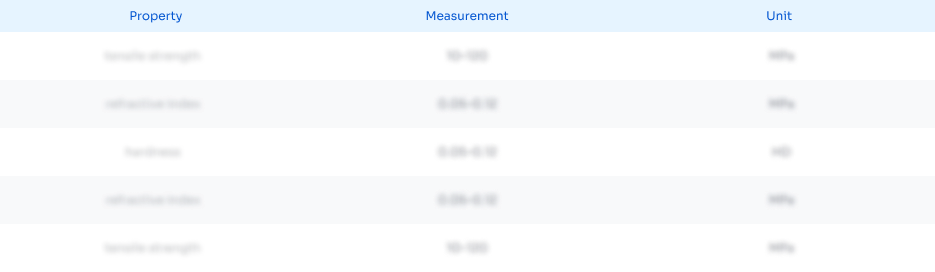
Abstract
Description
Claims
Application Information

- R&D
- Intellectual Property
- Life Sciences
- Materials
- Tech Scout
- Unparalleled Data Quality
- Higher Quality Content
- 60% Fewer Hallucinations
Browse by: Latest US Patents, China's latest patents, Technical Efficacy Thesaurus, Application Domain, Technology Topic, Popular Technical Reports.
© 2025 PatSnap. All rights reserved.Legal|Privacy policy|Modern Slavery Act Transparency Statement|Sitemap|About US| Contact US: help@patsnap.com