Plate material omnibearing locating structure and method in hot press forming technology
A technology of hot-pressing forming and positioning method, which is applied in positioning devices, manufacturing tools, metal processing equipment, etc., can solve the problems of inability to locate in four directions, instability, and damage to the surface of the forming block, so as to achieve accurate and convenient positioning and not easy to deform. wear effect
- Summary
- Abstract
- Description
- Claims
- Application Information
AI Technical Summary
Problems solved by technology
Method used
Image
Examples
Embodiment approach 1
[0029] This embodiment provides an all-round positioning structure and its all-round positioning method for sheet metal in the hot pressing forming process, such as figure 1 and 2 As shown, the above-mentioned all-round positioning structure is a raised circular flange hole extending from the plane of the sheet material 1. The circular flange hole and the sheet material 1 are integrally structured. The end 111 is higher than the blank 1 by a certain distance.
[0030] In this embodiment, before forming the above-mentioned circular flanging hole, firstly a circular pre-punching hole 12 will be processed at a preset position on the sheet material 1, and then the The flanging pin 3 processes the circular pre-punching hole 12 into the above-mentioned circular flanging hole, as figure 2 As shown, it can be seen that the side of the circular flanging hole is a vertical edge 13 of an overall structure, and the above-mentioned circular flanging hole can be used as the main positio...
Embodiment approach 2
[0038] This embodiment is a further improvement of Embodiment 1. The main improvement is that in Embodiment 1, a flanged pin 3 with a spherical pin head 31 is used, and a circle with a vertical edge 13 of an integral structure is formed. Shaped flanging hole, because the contact area between the limit inner side of this circular flanging hole and the flanging pin 3 is larger, so it is not easy to unload the flanging pin 3; The flanging pin 3 of head 32, the circular flanging hole that has the inclined edge 14 of integral structure that molding goes out, because the frictional force between the inclined edge 14 inner side of integral structure and flat head tapered pin head 32 is less, so can Use less force to remove the flange pin 3, such as image 3 and 4 shown.
[0039] Apart from this, this embodiment is completely the same as Embodiment 1, and will not be repeated here.
Embodiment approach 3
[0041]This embodiment is a further improvement of Embodiment 1. The main improvement is that the side of the circular flanged hole in Embodiment 1 is the vertical edge 13 of the overall structure. There is a defect in this circular flanged hole: when needed When the flanging pin 3 is removed, because the inner wall of the vertical edge 13 of the overall structure of the circular flanging hole is close to the pin body 33 of the flanging pin 3, the frictional force between the two is relatively large, and the flanging pin 3 It is not easy to remove; and the edge of the circular flanging hole in this embodiment is the vertical edge 114 of the multi-lobed structure (or zigzag structure, wave-shaped structure, etc.), of course, if the corresponding pre-punched hole is multi-lobed (or zigzag structure, wavy structure, etc.) pre-punching hole 17, the contact area between the inner wall of the vertical side 15 of the multi-lobe structure and the flanging pin 3 is reduced, and the frict...
PUM
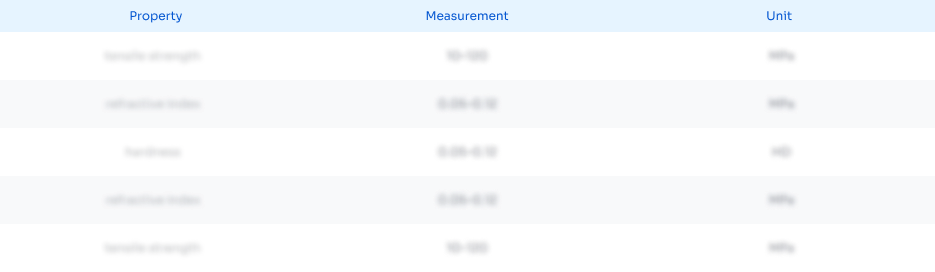
Abstract
Description
Claims
Application Information

- Generate Ideas
- Intellectual Property
- Life Sciences
- Materials
- Tech Scout
- Unparalleled Data Quality
- Higher Quality Content
- 60% Fewer Hallucinations
Browse by: Latest US Patents, China's latest patents, Technical Efficacy Thesaurus, Application Domain, Technology Topic, Popular Technical Reports.
© 2025 PatSnap. All rights reserved.Legal|Privacy policy|Modern Slavery Act Transparency Statement|Sitemap|About US| Contact US: help@patsnap.com