Method for in-line calibration of an industrial robot, calibration system for performing such a method and industrial robot comprising such a calibration system
A technology of industrial robots, calibration methods, applied in general control systems, control/regulation systems, instruments, etc.
- Summary
- Abstract
- Description
- Claims
- Application Information
AI Technical Summary
Problems solved by technology
Method used
Image
Examples
Embodiment Construction
[0057] In the following, the calibration system according to the invention is effectively described in detail. Calibration provides online compensation for inaccuracies in robotic applications. Furthermore, the system is portable, highly accurate, time-sensitive and cost-effective. In the following, methods and systems are described using the example of thermal compensation. Of course, the invention is not limited to the described example of thermal compensation. There are many sources of error that lead to inaccuracies in robot position, including manufacturing tolerances during production of the robot, thermal effects, encoder offset, compliance of the arms, gear transmission errors, and backlash in the gear transmission. All of these can be compensated for by the calibration method and system according to the invention.
[0058] Furthermore, the invention is not limited to a particular kind of two-dimensional optical position sensor, but any kind of suitable sensor, inde...
PUM
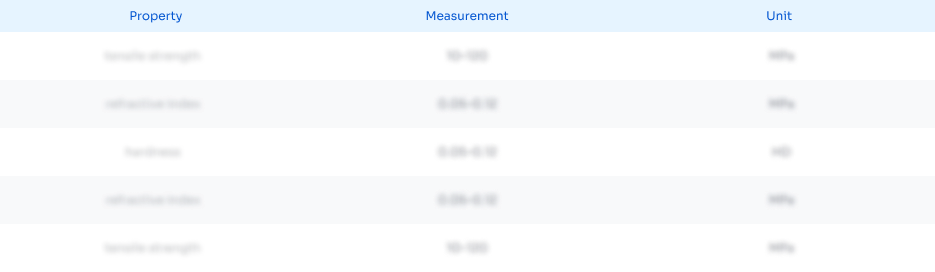
Abstract
Description
Claims
Application Information

- Generate Ideas
- Intellectual Property
- Life Sciences
- Materials
- Tech Scout
- Unparalleled Data Quality
- Higher Quality Content
- 60% Fewer Hallucinations
Browse by: Latest US Patents, China's latest patents, Technical Efficacy Thesaurus, Application Domain, Technology Topic, Popular Technical Reports.
© 2025 PatSnap. All rights reserved.Legal|Privacy policy|Modern Slavery Act Transparency Statement|Sitemap|About US| Contact US: help@patsnap.com