Soundproof-cotton gluing machine application method
A cotton gluing machine and gluing technology, applied in the field of gluing machine, can solve the problems of glue easily sticking at both ends of the rubber roller, and the glue is not easy to clean, and it is not easy to clean, so as to eliminate the phenomenon of glue failure, eliminate glue blocking, The effect of improving gluing efficiency
- Summary
- Abstract
- Description
- Claims
- Application Information
AI Technical Summary
Problems solved by technology
Method used
Image
Examples
Embodiment 1
[0059] Such as figure 1 As shown, the soundproof cotton gluing machine of the present embodiment includes a frame 1, and a gluing mechanism is provided on the frame 1, and the gluing mechanism includes a gluing roller 3, a gluing roller 4 and a gluing roller arranged in parallel to each other. Roller 5, the glue-coating roller 3 is located below the gap between the top glue roller 4 and the glue-adjusting roller 5; the glue-coating roller 3, the top glue roller 4 and the glue-adjusting roller 5 are driven to rotate by different driving motors 2; A rubber storage barrel 8 is arranged above the upper rubber roller 4 and the rubber adjustment roller 5 .
[0060] The outer side of the glue storage barrel 8 wraps the heating layer 801 and the insulation layer 802 respectively from the inside to the outside. The heating layer 801 is provided with a thermal resistor, which can heat the glue in the glue storage barrel 8 through the heat release of the thermal resistor; the insulation ...
PUM
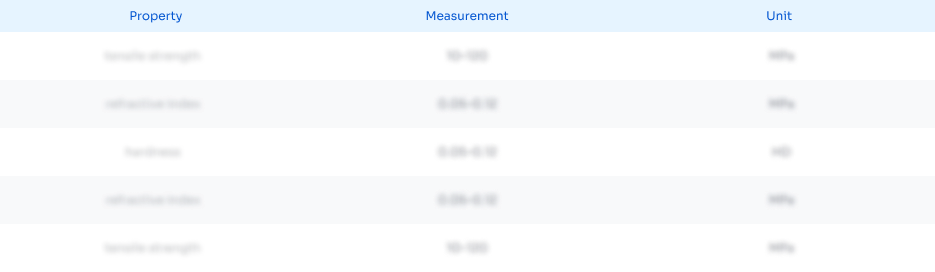
Abstract
Description
Claims
Application Information

- R&D Engineer
- R&D Manager
- IP Professional
- Industry Leading Data Capabilities
- Powerful AI technology
- Patent DNA Extraction
Browse by: Latest US Patents, China's latest patents, Technical Efficacy Thesaurus, Application Domain, Technology Topic, Popular Technical Reports.
© 2024 PatSnap. All rights reserved.Legal|Privacy policy|Modern Slavery Act Transparency Statement|Sitemap|About US| Contact US: help@patsnap.com