Method for recycling reduction coal from coal slime
A coal slime and magnetic separation technology, applied in chemical instruments and methods, wet separation, solid separation, etc., can solve the problems of insignificant reduction of coal slime ash content and difficulty in obtaining ash content, so as to improve the comprehensive utilization rate and improve the quality , The effect of saving the cost of medicine
- Summary
- Abstract
- Description
- Claims
- Application Information
AI Technical Summary
Problems solved by technology
Method used
Image
Examples
Embodiment 1
[0039] In this example, a certain coal slime in Yunnan with an ash content of 55.6%, a total sulfur content of 0.85% and a fixed carbon of 28.6% is used as the raw material, and the process of recovering the reduced coal is as follows: image 3 The specific steps are as follows:
[0040] S11: First add water to slurry the above-mentioned coal slime, use a high-frequency vibrating screen for classification, and then ball mill the coarse particles, and then enter the next process together with the fine particles. Ingredients account for 90%;
[0041] S12: First perform weak magnetic separation on the pulp obtained in step S11, the magnetic induction intensity is 0.08T, to obtain iron concentrate and weak magnetic tailings with an iron content greater than 60%; and then perform strong magnetic separation on the weak magnetic tailings , the magnetic induction intensity is 1.0T, and the magnetic separation concentrate and magnetic separation tailings are obtained;
[0042] S13: T...
Embodiment 2
[0045] In this embodiment, a certain coal slime with an ash content of 49.8% and a sulfur content of 0.97% in Hebei is used as the raw material, and the process of recovering the reduced coal from it is as follows: Figure 4 The specific steps are as follows:
[0046] S21: First add water to slurry the above-mentioned coal slime, use a cyclone for classification, and then ball mill the coarse particles to control the slurry concentration of 40% and the slurry fineness of -0.075mm to account for 70% of the ingredients. The ball mill discharges and fine particles Go to the next step together;
[0047] S22: send the ore pulp obtained in step S21 into a strong magnetic separator for magnetic separation, the magnetic induction intensity is 0.9T, and then introduce the magnetic separation tailings into the thickening device, and control the discharge concentration to be 25%;
[0048] S23: Introduce the ore pulp obtained in step S22 into the mixing tank, add flotation reagents, and ...
Embodiment 3
[0051] In the present embodiment, the coal slime with a certain ash content of 47.8% and a total sulfur content of 1.22% in Shanxi is used as a raw material, and the concrete steps of recovering the reduced coal are as follows:
[0052] S31: First add water to slurry the above-mentioned coal slime, use a cyclone for classification, and then enter the coarse particles into the wet ball mill and enter the next process together with the fine particles, and control the composition of the slurry concentration of 32% and the pulp fineness of -0.075mm 78%;
[0053] S32: introduce the ore pulp obtained in step S31 into a strong magnetic magnetic separator for magnetic separation, the magnetic induction intensity is 1.8T, then the magnetic separation concentrate is post-processed to recover valuable components, and the magnetic separation tailings enter the next process;
[0054] S33: The magnetic separation tailings obtained in step S32 are introduced into the thickening device, and t...
PUM
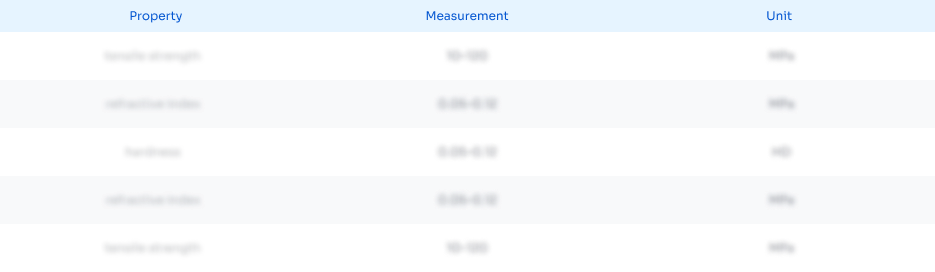
Abstract
Description
Claims
Application Information

- R&D Engineer
- R&D Manager
- IP Professional
- Industry Leading Data Capabilities
- Powerful AI technology
- Patent DNA Extraction
Browse by: Latest US Patents, China's latest patents, Technical Efficacy Thesaurus, Application Domain, Technology Topic, Popular Technical Reports.
© 2024 PatSnap. All rights reserved.Legal|Privacy policy|Modern Slavery Act Transparency Statement|Sitemap|About US| Contact US: help@patsnap.com