Supporting device and machining precision improving method for thin-wall part
A support device and processing precision technology, applied in positioning devices, metal processing equipment, metal processing machinery parts, etc., can solve problems such as influence, large image fluctuations, and influence parameter selection
- Summary
- Abstract
- Description
- Claims
- Application Information
AI Technical Summary
Problems solved by technology
Method used
Image
Examples
Embodiment Construction
[0057] One, the embodiment of device of the present invention:
[0058] Such as figure 1 , 2 As shown, a support device for thin-walled parts includes a support platform 3, a first loop 1, a second loop 2, an X-direction slide 5, a matching buckle 4 with a through hole 6, and a first slide 7 -1, the second slideway 7-2, the third slideway 8-1, the fourth slideway 8-2 and the supporting mechanism for fixing and supporting the thin-walled parts; the first loop 1 and the second loop 2 concentrically and sequentially arranged on the support platform 3, the X-direction slideway 5 is arranged on the support platform 3 and passes through the center of the first loop 1 and the second loop 2, the first slideway 7-1 and The second slideway 7-2 is symmetrically arranged on both sides of the X-direction slideway 5, the third slideway 8-1 and the fourth slideway 8-2 are symmetrically arranged on both sides of the X-direction slideway 5, and the matching buckle 4 Set at the intersection ...
PUM
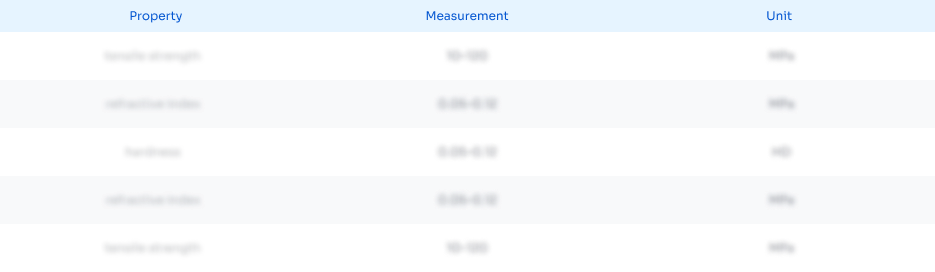
Abstract
Description
Claims
Application Information

- Generate Ideas
- Intellectual Property
- Life Sciences
- Materials
- Tech Scout
- Unparalleled Data Quality
- Higher Quality Content
- 60% Fewer Hallucinations
Browse by: Latest US Patents, China's latest patents, Technical Efficacy Thesaurus, Application Domain, Technology Topic, Popular Technical Reports.
© 2025 PatSnap. All rights reserved.Legal|Privacy policy|Modern Slavery Act Transparency Statement|Sitemap|About US| Contact US: help@patsnap.com