Marine crane controller based on an input shaping technology
A marine crane, input shaping technology, applied in the direction of transportation and packaging, load hanging components, etc., can solve the problems of reducing production efficiency, increasing work costs, etc., to achieve the effect of improving work efficiency, easy to implement, and simple methods
- Summary
- Abstract
- Description
- Claims
- Application Information
AI Technical Summary
Problems solved by technology
Method used
Image
Examples
Embodiment Construction
[0022] combine figure 1 In the physical model of a marine crane, the residual swing of the load can be expressed as the swing angle θ in the plane of the boom 1 and the swing angle θ out of the plane of the boom 2 . Let the mass of the load be m and the length of the boom be L B , the length of the rope is L, the included angle between the boom plane and the horizontal axis of the marine crane (i.e. the X axis) is the rotation angle α, and the included angle between the boom plane and the vertical axis of the marine crane (i.e. the Z axis) is the pitch angle β, then The position of the boom tip in the inertial coordinate system is
[0023] x bt = L B cos α sin β ...
PUM
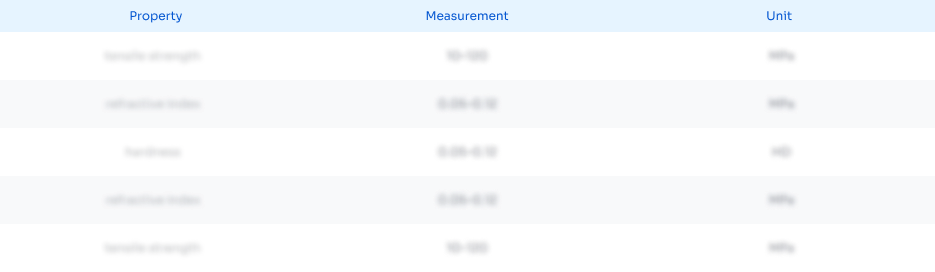
Abstract
Description
Claims
Application Information

- R&D
- Intellectual Property
- Life Sciences
- Materials
- Tech Scout
- Unparalleled Data Quality
- Higher Quality Content
- 60% Fewer Hallucinations
Browse by: Latest US Patents, China's latest patents, Technical Efficacy Thesaurus, Application Domain, Technology Topic, Popular Technical Reports.
© 2025 PatSnap. All rights reserved.Legal|Privacy policy|Modern Slavery Act Transparency Statement|Sitemap|About US| Contact US: help@patsnap.com