High-frequency rotary precision-forging compounding method for metal composite tube and rod manufacturing
A technology of metal composite pipes and metal pipes, which is applied in the direction of manufacturing tools, metal processing equipment, hammer driving devices, etc., can solve the problems of poor bonding strength of composite steel pipes, fast wear of hammer heads, low efficiency, etc., and achieve smooth product appearance The effect of high precision, low site requirements and short process flow
- Summary
- Abstract
- Description
- Claims
- Application Information
AI Technical Summary
Problems solved by technology
Method used
Image
Examples
Embodiment Construction
[0025] The present invention and its beneficial technical effects will be further described in detail below in conjunction with the accompanying drawings and preferred embodiments.
[0026] see figure 1 , a high-frequency rotary precision forging composite method for the manufacture of metal composite tubes and rods, which mainly includes the following process steps: (1) Clean the workpiece, and clean the surface of the metal tube / metal rod to be composited by physical or chemical processes; (2) ) Composite preparation, put the outer metal tube on the metal tube / metal rod as the inner liner / liner rod, and fix and position the two ends of the outer metal tube with the metal tube / metal rod to form a compound to be compounded Metal composite pipe / rod; if the inner liner is a metal pipe, a core rod needs to be inserted into the metal pipe; (3) Forging and compounding, the metal composite pipe / rod to be composited is placed in a high-frequency rotary precision forging machine The ...
PUM
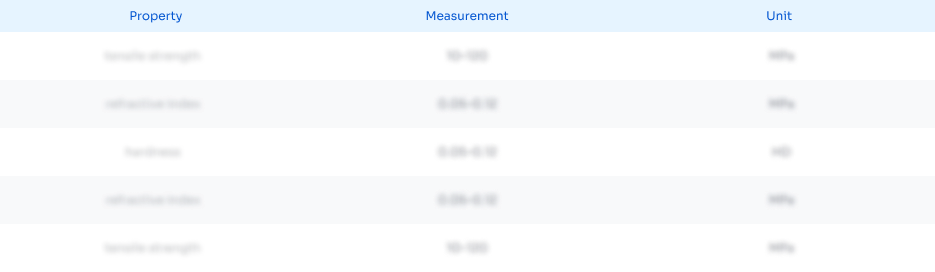
Abstract
Description
Claims
Application Information

- R&D
- Intellectual Property
- Life Sciences
- Materials
- Tech Scout
- Unparalleled Data Quality
- Higher Quality Content
- 60% Fewer Hallucinations
Browse by: Latest US Patents, China's latest patents, Technical Efficacy Thesaurus, Application Domain, Technology Topic, Popular Technical Reports.
© 2025 PatSnap. All rights reserved.Legal|Privacy policy|Modern Slavery Act Transparency Statement|Sitemap|About US| Contact US: help@patsnap.com