A centrifugal molding method for preparing transparent ceramic laser rods
A transparent ceramic, centrifugal molding technology, applied in the direction of active medium materials, etc., can solve the problems of affecting the transmittance of the final sample, difficult to remove bubbles, difficult to remove impurities, etc., to reduce the difficulty of preparation, reduce open porosity, and outstanding optical properties. Effect
- Summary
- Abstract
- Description
- Claims
- Application Information
AI Technical Summary
Problems solved by technology
Method used
Image
Examples
Embodiment 1
[0032] (1) According to the chemical formula (Y 0.95 Yb 0.05 ) 3 al 5 o 12 The stoichiometric ratio will be Al 2 o 3 , Y 2 o 3 , Yb 2 o 3 Mix the powders, then add a dispersant with a mass of 2-4% of the mass of the mixed powder and tetraethyl orthosilicate with a mass of 0.3-0.6% of the mass of the mixed powder as a sintering aid, put the above powder into the In a ball milling tank with corundum grinding balls, use absolute ethanol as the dispersion medium for ball milling for 14-18 hours, then place the slurry in an oven to dry, and the dried powder is calcined at 1100°C to obtain a uniformly mixed raw material powder;
[0033] (2) The volume of the slurry to be configured is 30ml, the volume of the raw material powder accounts for 20% of the total volume of the slurry, and the mass of ammonium polyacrylate is 4% of the mass of the powder. After calculation, 27.57g of the raw material powder, 2.2ml of Dispex A40 and Put 22ml of deionized water into a ball mill tan...
Embodiment 2
[0044] (1) According to the chemical formula (Y 0.9 Yb 0.1 ) 3 al 5 o 12 The stoichiometric ratio will be Al 2 o 3 , Y 2 o 3 , Yb 2 o 3 Mix the powders, then add a dispersant with a mass of 2-4% of the mass of the mixed powder and tetraethyl orthosilicate with a mass of 0.3-0.6% of the mass of the mixed powder as a sintering aid, put the above powder into the In a ball milling tank with corundum grinding balls, use absolute ethanol as the dispersion medium for ball milling for 14-18 hours, then place the slurry in an oven to dry, and the dried powder is calcined at 1100°C to obtain a uniformly mixed raw material powder;
[0045] (2) The volume of the slurry to be configured is 30ml, the volume of the raw material powder accounts for 20% of the total volume of the slurry, and the mass of ammonium polyacrylate is 2% of the mass of the powder. After calculation, 28.01g of the raw material powder, 1.1ml of Dispex A40 and Put 23ml of deionized water into a ball mill tank ...
Embodiment 3
[0056] (1) According to the chemical formula (Y 0.98 Yb 0.02 ) 3 al 5 o 12 The stoichiometric ratio will be Al 2 o 3 , Y 2 o 3 , Yb 2 o 3 Mix the powders, then add a dispersant with a mass of 2-4% of the mass of the mixed powder and tetraethyl orthosilicate with a mass of 0.3-0.6% of the mass of the mixed powder as a sintering aid, put the above powder into the In a ball milling tank with corundum grinding balls, use absolute ethanol as the dispersion medium for ball milling for 14-18 hours, then place the slurry in an oven to dry, and the dried powder is calcined at 1100°C to obtain a uniformly mixed raw material powder;
[0057] (2) The volume of the slurry to be configured is 30ml, the volume of the raw material powder accounts for 20% of the total volume of the slurry, and the mass of ammonium polyacrylate is 3% of the mass of the powder. After calculation, 27.54g of the raw material powder, 1.7ml of Dispex A40 and Put 22ml of deionized water into a ball mill jar...
PUM
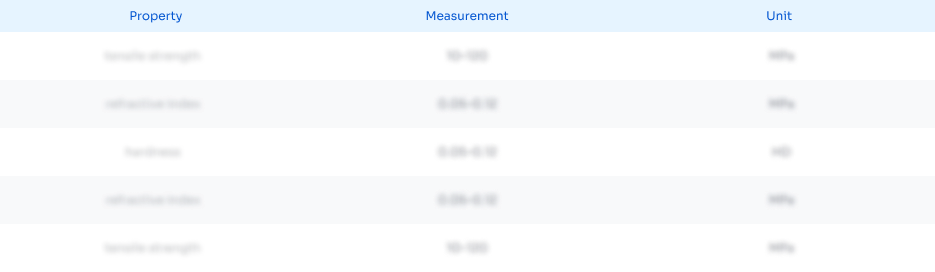
Abstract
Description
Claims
Application Information

- R&D
- Intellectual Property
- Life Sciences
- Materials
- Tech Scout
- Unparalleled Data Quality
- Higher Quality Content
- 60% Fewer Hallucinations
Browse by: Latest US Patents, China's latest patents, Technical Efficacy Thesaurus, Application Domain, Technology Topic, Popular Technical Reports.
© 2025 PatSnap. All rights reserved.Legal|Privacy policy|Modern Slavery Act Transparency Statement|Sitemap|About US| Contact US: help@patsnap.com