A combined method for deep desulfurization of liquefied gas
A combined method and deep desulfurization technology, applied in chemical instruments and methods, separation methods, gas fuels, etc., can solve problems such as insufficient oxidation, large lye consumption, and reduced extraction capacity, and achieve cleanliness and deep desulfurization The effect of high height and small footprint
- Summary
- Abstract
- Description
- Claims
- Application Information
AI Technical Summary
Problems solved by technology
Method used
Image
Examples
Embodiment
[0027] In the lye regeneration scale-up test with 50L / h lye treatment capacity, the lye regeneration test and the exhaust gas absorption test were carried out at the same time. In the lye regeneration test, the gas-liquid volume ratio ranges from 1 to 1500:1, and the reaction temperature is 20 to 70°C. In the exhaust gas absorption test, the diesel flow rate is 0.5~5L / h, and the reaction temperature is 20~40℃.
[0028] The lye is introduced into the heating tank from the storage tank, and after heat exchange with steam, it is pumped into the supergravity reactor, and the air is sent into the supergravity reactor by the fan. Air and waste lye are mixed in the overweight machine, the tail gas is separated by the liquid trap and then enters the absorption device. After regeneration, the lye is sampled and stored in a 1m3 barrel. The lye flow is controlled by the rotameter and the bypass valve, the air flow is controlled by the rotameter, and the speed of the overweight machine i...
PUM
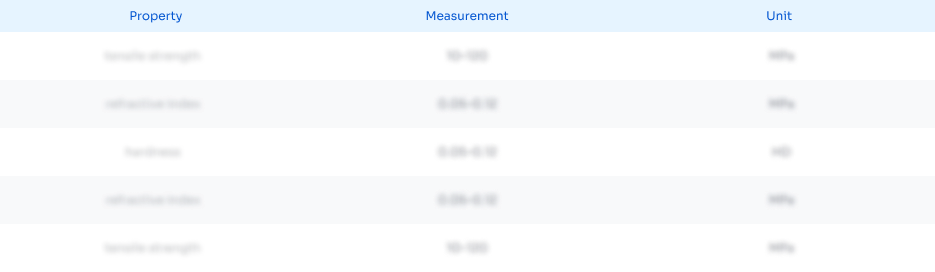
Abstract
Description
Claims
Application Information

- Generate Ideas
- Intellectual Property
- Life Sciences
- Materials
- Tech Scout
- Unparalleled Data Quality
- Higher Quality Content
- 60% Fewer Hallucinations
Browse by: Latest US Patents, China's latest patents, Technical Efficacy Thesaurus, Application Domain, Technology Topic, Popular Technical Reports.
© 2025 PatSnap. All rights reserved.Legal|Privacy policy|Modern Slavery Act Transparency Statement|Sitemap|About US| Contact US: help@patsnap.com