Multi-freedom-degree parallel mechanism type controllable mobile welding robot
A welding robot and mechanism technology, applied in the field of robots, can solve the problems of small working space of parallel robots, unsolved industrial robots, complex structure, etc., and achieve the effects of force and torque, increased working space, and small motion inertia.
- Summary
- Abstract
- Description
- Claims
- Application Information
AI Technical Summary
Problems solved by technology
Method used
Image
Examples
Embodiment Construction
[0047] A multi-degree-of-freedom parallel mechanism controllable mobile welding robot of the present invention will be further described below in conjunction with the accompanying drawings and specific embodiments.
[0048] see Figure 1 to Figure 11, is a multi-degree-of-freedom parallel mechanism controllable mobile welding robot of the present invention, including a mobile platform 1, a fuselage 2, a first connecting rod 3, a second connecting rod 7, a third connecting rod 5, and a fourth connecting rod 20 , the fifth connecting rod 23, the sixth connecting rod 21, the seventh connecting rod 11, the eighth connecting rod 12, the ninth connecting rod 18, the tenth connecting rod 14, the eleventh connecting rod 15, the twelfth connecting rod 26 , the thirteenth connecting rod 27, the fourteenth connecting rod 29, the end effector 30;
[0049] The mobile platform 1 is moved by wheels mounted on its bottom;
[0050] The seventh connecting rod 11 is sequentially provided with ...
PUM
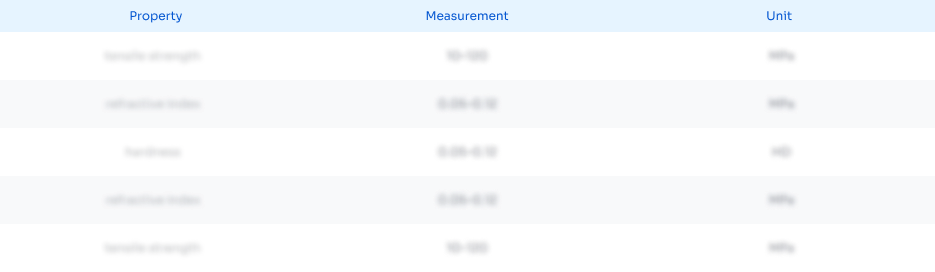
Abstract
Description
Claims
Application Information

- R&D Engineer
- R&D Manager
- IP Professional
- Industry Leading Data Capabilities
- Powerful AI technology
- Patent DNA Extraction
Browse by: Latest US Patents, China's latest patents, Technical Efficacy Thesaurus, Application Domain, Technology Topic, Popular Technical Reports.
© 2024 PatSnap. All rights reserved.Legal|Privacy policy|Modern Slavery Act Transparency Statement|Sitemap|About US| Contact US: help@patsnap.com