Final drive positioner manufacturing process method
A technology of the main reducer locator and manufacturing process, which is applied in the directions of aircraft parts, transportation and packaging, etc. It can solve the problems of positioning and installation deviation of aircraft main reducer joint products, achieve the effect of no deviation in positioning and installation, and avoid the effect of positioning and installation deviation
- Summary
- Abstract
- Description
- Claims
- Application Information
AI Technical Summary
Problems solved by technology
Method used
Image
Examples
Embodiment
[0051] The length of the positioning sleeve 1 of the main subtractive locator is 60 millimeters, and the inner hole size of the positioning sleeve 1 is mm, the outer circle size of positioning sleeve 1 is mm, the inner diameter of the through hole 5 is mm, the outer diameter of the disc 2 is mm, the thickness of the joint plate 2 is 12 mm, and the inner diameter of the cursor hole 6 is mm, the inner diameter of positioning hole 7 is mm, the width of the positioning groove 8 is 22H7 mm, the thickness of the fork ear 3 is 46H7 mm, the thickness of the ear piece of the fork ear 3 is 12H7 mm, and the vertical distance between the center of the through hole 5 and the center of the cursor hole 6 is 71.48 ±0.02 mm, the horizontal distance between the center of the through hole 5 and the center of the cursor hole 6 is 14.40 ± 0.02 mm, the vertical distance between the center of the through hole 5 and the center of the positioning hole 7 is 106 ± 0.02 mm, the center of the thr...
PUM
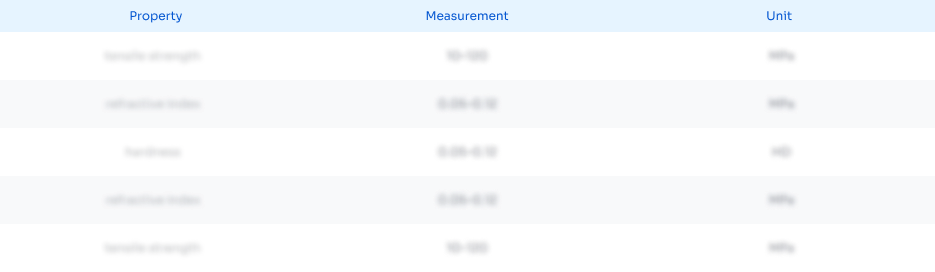
Abstract
Description
Claims
Application Information

- R&D
- Intellectual Property
- Life Sciences
- Materials
- Tech Scout
- Unparalleled Data Quality
- Higher Quality Content
- 60% Fewer Hallucinations
Browse by: Latest US Patents, China's latest patents, Technical Efficacy Thesaurus, Application Domain, Technology Topic, Popular Technical Reports.
© 2025 PatSnap. All rights reserved.Legal|Privacy policy|Modern Slavery Act Transparency Statement|Sitemap|About US| Contact US: help@patsnap.com