A kind of preparation method of ultrahigh-purity amorphous spherical silica powder
A technology of spherical silicon micropowder and amorphous state, applied in the direction of silicon oxide, silicon dioxide, etc., can solve the problems of high equipment cost, low spheroidization rate, corrosion of metal equipment, etc., and achieve uniform particle size distribution, high spheroidal rate, and dispersed high degree of effect
- Summary
- Abstract
- Description
- Claims
- Application Information
AI Technical Summary
Problems solved by technology
Method used
Image
Examples
Embodiment 1
[0028] Mix 30g of purified tetramethoxysilane (TMOS) with 4g of pure water and a small amount of hydrochloric acid evenly. After the reaction is completed, methanol is distilled off to obtain a silane polymer. Add 100g of pure water and 4g of Tween to the prepared silane polymer. -80 and 0.2g polyether modified silicone oil, stir well with a mixer, emulsify with a homogeneous emulsifier for 10 minutes, add 4g of 25% ammonia water and stir for 3 hours, and add the filter cake obtained by vacuum filtration to an aqueous solution containing 8% ammonia water Reflux for 2 hours, filter and wash with ethanol twice, dry at 80°C for 6h, and calcined at 900°C for 1 hour to obtain spherical silica powder.
[0029] The spherical silica powder prepared by the above steps is analyzed by X-ray diffraction to be pure amorphous silica, and no crystallization occurs when calcined at 900 °C; the particle size distribution is uniform as shown in Figure 1, and the median diameter of the silica pow...
Embodiment 2
[0034]Mix 20g of purified tetraethoxysilane (TEOS) with 3g of pure water and a small amount of nitric acid evenly. After the reaction is completed, distill off ethanol to obtain a silane polymer. Add 100g of pure water and 2g of Op-10 to the silane polymer and 0.1g of silicone antifoaming agent, stir evenly with a mixer, emulsify with a homogeneous emulsifier for 30 minutes, add 5g of 15% tetramethylammonium hydroxide, stir for 4 hours, and centrifuge to obtain SiO 2 The microspheres were added to an aqueous solution containing 10% tetramethylammonium hydroxide and refluxed for 3 hours. After centrifugation, they were washed 3 times with propylene glycol monomethyl ether, dried at 100 °C for 6 hours, and calcined at 1000 °C for 1 hour to obtain spherical silica powder. .
[0035] The spherical silicon micropowder prepared by the above steps is analyzed by X-ray diffraction to be pure amorphous silica, and no crystallization occurs when calcined at 1000 ℃; the particle size ...
PUM
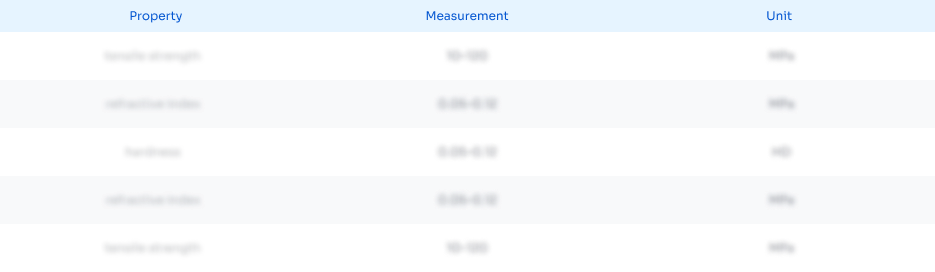
Abstract
Description
Claims
Application Information

- R&D
- Intellectual Property
- Life Sciences
- Materials
- Tech Scout
- Unparalleled Data Quality
- Higher Quality Content
- 60% Fewer Hallucinations
Browse by: Latest US Patents, China's latest patents, Technical Efficacy Thesaurus, Application Domain, Technology Topic, Popular Technical Reports.
© 2025 PatSnap. All rights reserved.Legal|Privacy policy|Modern Slavery Act Transparency Statement|Sitemap|About US| Contact US: help@patsnap.com