Novel temperature difference control structure for firing equipment
A new type of temperature control technology, applied in lighting and heating equipment, furnace types, furnaces, etc., to solve problems such as waste, cracking, product deformation, etc.
- Summary
- Abstract
- Description
- Claims
- Application Information
AI Technical Summary
Problems solved by technology
Method used
Image
Examples
Embodiment Construction
[0009] The present invention will be further described below in conjunction with specific embodiment:
[0010] See attached figure 1 As shown, a novel temperature difference control structure for firing equipment described in this embodiment includes a kiln frame 1, a roller conveying assembly 3 installed on the kiln frame 1, and a The transmission mechanism 2 that drives the roller conveying assembly 3 to rotate, multiple sets of combustion splitter assemblies 4 that are symmetrically installed on both sides of the kiln frame and arranged along the conveying direction of the roller conveying assembly 3, and are used to feed the combustion splitter assembly 4 burners 6 for providing heat. Each set of combustion splitter assembly 4 includes a pair of combustion splitter groups 410 installed on the upper and lower sides of the roller conveying assembly 3 respectively, wherein each combustion splitter group 410 also includes a burner for firing the adjacent kiln on the roller co...
PUM
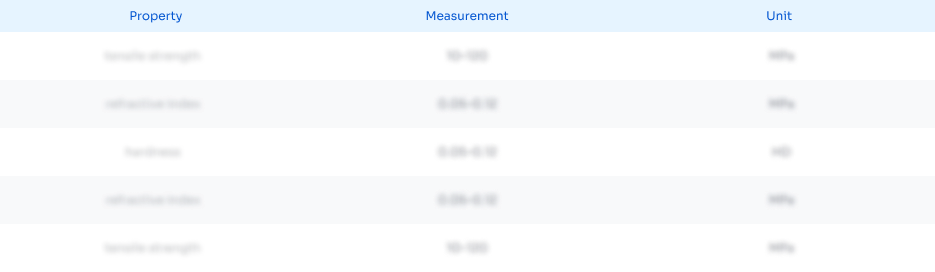
Abstract
Description
Claims
Application Information

- R&D
- Intellectual Property
- Life Sciences
- Materials
- Tech Scout
- Unparalleled Data Quality
- Higher Quality Content
- 60% Fewer Hallucinations
Browse by: Latest US Patents, China's latest patents, Technical Efficacy Thesaurus, Application Domain, Technology Topic, Popular Technical Reports.
© 2025 PatSnap. All rights reserved.Legal|Privacy policy|Modern Slavery Act Transparency Statement|Sitemap|About US| Contact US: help@patsnap.com