A full grouting sleeve for steel bar connection
A grouting sleeve and full grouting technology, which is applied in the direction of structural elements, building components, building reinforcements, etc., can solve the problems of restricting the application of prefabricated frame structures or technological development, and achieve high processing costs, improve project quality, and shorten lengths Effect
- Summary
- Abstract
- Description
- Claims
- Application Information
AI Technical Summary
Problems solved by technology
Method used
Image
Examples
Embodiment
[0029] Such as figure 1 , 4 As shown in and 9, the full grouting sleeve 1 for connecting steel bars in this embodiment includes two grouting sleeves, the first grouting sleeve 11 and the second grouting sleeve 12, the first grouting sleeve 11 or the second The grout barrel 12 is provided with a grout discharge hole 2. The two grouting sleeves are connected by threaded connection or by the connecting sleeve 5. The two grouting sleeves are respectively poured into the first grouting sleeve 11 and the second grouting sleeve 12 The grouting material is fixedly connected with the connected steel bars 4.
[0030] Such as Figure 1-3 As shown, the outer diameters of the two grouting sleeves are different, the outer diameter of the first grouting sleeve 11 is greater than the outer diameter of the second grouting sleeve 12, and the two grouting sleeves are connected by straight threads or taper threads to form a stepped shape. Split type full grouting sleeve 1.
[0031] Such as Figure 1-...
PUM
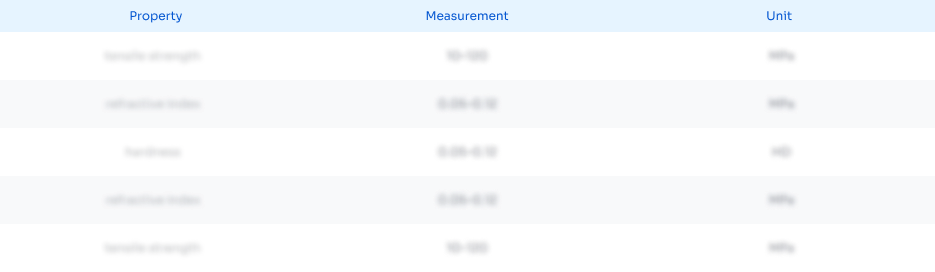
Abstract
Description
Claims
Application Information

- R&D Engineer
- R&D Manager
- IP Professional
- Industry Leading Data Capabilities
- Powerful AI technology
- Patent DNA Extraction
Browse by: Latest US Patents, China's latest patents, Technical Efficacy Thesaurus, Application Domain, Technology Topic, Popular Technical Reports.
© 2024 PatSnap. All rights reserved.Legal|Privacy policy|Modern Slavery Act Transparency Statement|Sitemap|About US| Contact US: help@patsnap.com