Automobile CAN bus system and its short-circuit control method
A CAN bus, short-circuit control technology, applied in vehicle components, circuits or fluid pipelines, transportation and packaging, etc., can solve problems such as hidden safety hazards, long twisted pairs, and the controller cannot communicate normally.
- Summary
- Abstract
- Description
- Claims
- Application Information
AI Technical Summary
Problems solved by technology
Method used
Image
Examples
Embodiment Construction
[0030] In order to enable those skilled in the art to better understand the technical solutions of the present invention, the present invention will be further described in detail with reference to the accompanying drawings.
[0031] Such as figure 1 As shown, an automotive CAN bus system provided by an embodiment of the present invention includes a power twisted pair 1, a body twisted pair 2, an engine ECU 3, and a body controller 4. The power twisted pair 1 is electrically connected to the body twisted pair 2 , The engine ECU3 is electrically connected to the power twisted pair 1, and the body controller 4 is electrically connected to the body twisted pair 2. It also includes a voltage detection unit 6 and an automatic switch unit 7. The voltage detection unit 6 is respectively connected to the body twisted pair 2 and the body The controller 4 is electrically connected, and the automatic switch unit 7 is electrically connected to the power twisted pair 1 and the body controller ...
PUM
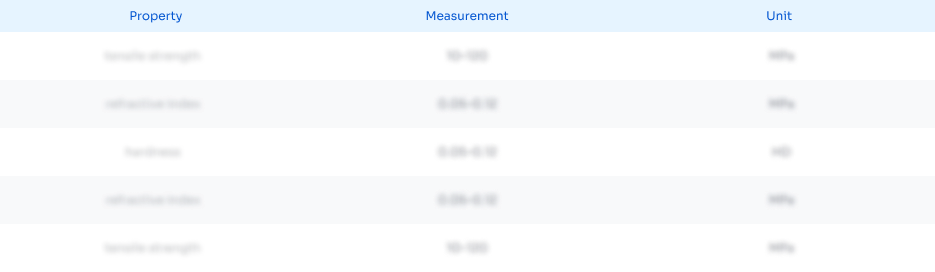
Abstract
Description
Claims
Application Information

- R&D
- Intellectual Property
- Life Sciences
- Materials
- Tech Scout
- Unparalleled Data Quality
- Higher Quality Content
- 60% Fewer Hallucinations
Browse by: Latest US Patents, China's latest patents, Technical Efficacy Thesaurus, Application Domain, Technology Topic, Popular Technical Reports.
© 2025 PatSnap. All rights reserved.Legal|Privacy policy|Modern Slavery Act Transparency Statement|Sitemap|About US| Contact US: help@patsnap.com