A prefabricated roof and its manufacturing method
A technology of prefabricated assembly and manufacturing methods, applied in the direction of roof insulation materials, roofs, roof coverings, etc., can solve the problems of poor strength, unsuitable for prefabricated roofs, and low seismic resistance, and achieve high seismic performance, convenient hoisting, Good waterproof effect
- Summary
- Abstract
- Description
- Claims
- Application Information
AI Technical Summary
Problems solved by technology
Method used
Image
Examples
Embodiment Construction
[0023] Such as figure 1 , figure 2 , image 3 As shown, a prefabricated roof is composed of modular roof panels 1 and surrounding roof strips 2 , and the roof panels 1 are inclined towards the surrounding roof strips 2 .
[0024] Both the roof slab 1 and the roof strip 2 are composed of a concrete layer 3 and a steel frame layer 4, and the steel frame layer 4 is made by bending shaped steel or steel plates. In this embodiment, the steel frame layer 4 preferably adopts a channel-shaped steel plate, and the channel-shaped The opening of the steel plate faces the concrete layer 3, and both ends of the upper part of the channel-shaped steel plate are prefabricated in the concrete layer 3. Insulation material is installed inside the steel frame layer 4, which reduces the heat transfer inside and outside the roof, and is conducive to building energy saving. A screw seat 8 is prefabricated on the concrete layer 3 of the roof strip 2, and the screw seat 8 can be used as a hoisting...
PUM
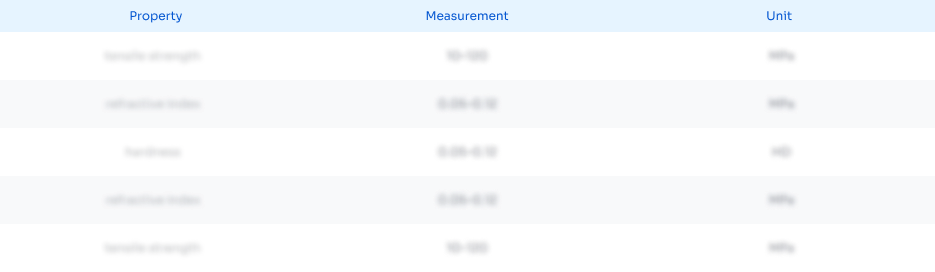
Abstract
Description
Claims
Application Information

- R&D
- Intellectual Property
- Life Sciences
- Materials
- Tech Scout
- Unparalleled Data Quality
- Higher Quality Content
- 60% Fewer Hallucinations
Browse by: Latest US Patents, China's latest patents, Technical Efficacy Thesaurus, Application Domain, Technology Topic, Popular Technical Reports.
© 2025 PatSnap. All rights reserved.Legal|Privacy policy|Modern Slavery Act Transparency Statement|Sitemap|About US| Contact US: help@patsnap.com