Glass kiln flue gas dust removal and denitration integrated process and device
A glass kiln and denitrification technology, applied in the direction of climate change adaptation, climate sustainability, human health protection, etc., can solve the problem that the electrostatic precipitator is difficult to achieve the dust removal effect, the alkali metal dust is very viscous and difficult to remove, and the increase in denitrification operating costs, etc. problem, to avoid poisoning and abrasion, high strength, reduce system investment cost and operating cost
- Summary
- Abstract
- Description
- Claims
- Application Information
AI Technical Summary
Problems solved by technology
Method used
Image
Examples
Embodiment Construction
[0025] Below in conjunction with accompanying drawing and specific embodiment the present invention is described in further detail:
[0026] This specific embodiment provides an integrated glass kiln flue gas dedusting and denitrification process. After the reducing agent ammonia is sprayed into the inlet flue by the ammonia injection mixing device 2, the ammonia is fully mixed with the original flue gas. After the mixed flue gas enters the dust removal and denitration chamber 4 of the device from the inlet flue 1 and the inlet horn 3, it passes through the mixed flue gas balance plate 8 and evenly passes through the dust removal and denitration catalyst 6 installed in the dust removal and denitration chamber 4, and the dust is collected by the outer layer of dust removal filter material 6-1 blocks and adheres to the surface of the filter material to form a dust filter layer. The mixed flue gas containing ammonia and nitrogen oxides enters the inner SCR catalyst 6-3 through the...
PUM
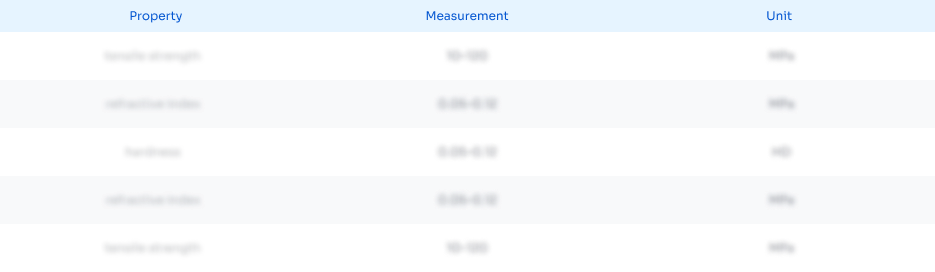
Abstract
Description
Claims
Application Information

- R&D Engineer
- R&D Manager
- IP Professional
- Industry Leading Data Capabilities
- Powerful AI technology
- Patent DNA Extraction
Browse by: Latest US Patents, China's latest patents, Technical Efficacy Thesaurus, Application Domain, Technology Topic, Popular Technical Reports.
© 2024 PatSnap. All rights reserved.Legal|Privacy policy|Modern Slavery Act Transparency Statement|Sitemap|About US| Contact US: help@patsnap.com