Finite element model correction method based on positive substructure
A technology of model correction and substructure, applied in instrumentation, calculation, electrical and digital data processing, etc., can solve problems such as difficulty in cooperating with real-time health monitoring and status assessment, long calculation time, and many uncertain parameters.
- Summary
- Abstract
- Description
- Claims
- Application Information
AI Technical Summary
Problems solved by technology
Method used
Image
Examples
Embodiment Construction
[0062] In order to make the object, technical solution and advantages of the present invention clearer, the present invention will be further described in detail below in conjunction with the accompanying drawings and embodiments. It should be understood that the specific embodiments described here are only used to explain the present invention, not to limit the present invention. In addition, the technical features involved in the various embodiments of the present invention described below can be combined with each other as long as they do not constitute a conflict with each other.
[0063] Divide the finite element model of the overall structure into multiple independent substructure finite element models, and solve the eigensolution and sensitivity matrix of the overall structure by solving one or several changed independent substructure eigensolutions and their sensitivity matrices, and use them in the finite element model Correction and damage identification. The so-cal...
PUM
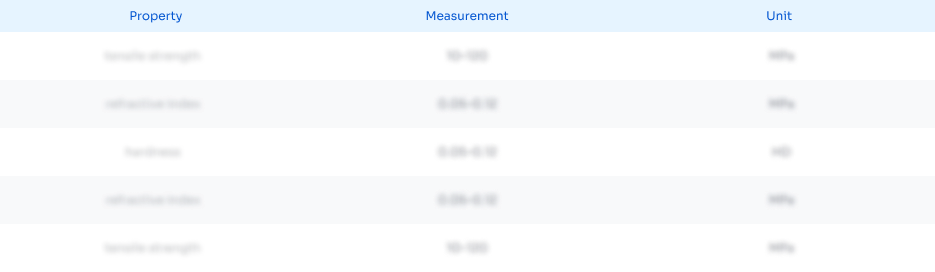
Abstract
Description
Claims
Application Information

- R&D
- Intellectual Property
- Life Sciences
- Materials
- Tech Scout
- Unparalleled Data Quality
- Higher Quality Content
- 60% Fewer Hallucinations
Browse by: Latest US Patents, China's latest patents, Technical Efficacy Thesaurus, Application Domain, Technology Topic, Popular Technical Reports.
© 2025 PatSnap. All rights reserved.Legal|Privacy policy|Modern Slavery Act Transparency Statement|Sitemap|About US| Contact US: help@patsnap.com