Steel coating device and production method thereof
A coating and steel plate technology, applied in coating, hot-dip coating process, metal material coating process, etc., can solve the problems of increased investment and plant construction, increased production line length, and difficult heating of thick materials, etc., to solve serious pollution , reduce steel consumption, and reduce repetitive construction problems
- Summary
- Abstract
- Description
- Claims
- Application Information
AI Technical Summary
Problems solved by technology
Method used
Image
Examples
Embodiment 1
[0041] A coating device includes: a base 1, a molten pool body, a molten basket body, a roller and a guide plate module, a sealing cover body, a roller rotating motor 6, and a transmission 7, and the molten pool body includes: a thermal insulation layer 2, a heating Layer 3, the inner wall of the molten pool 4, the agent discharge valve 5, the outermost layer of the molten pool body is the insulation layer 2, the middle layer is the heating layer 3, the innermost layer is the inner wall of the molten pool 4, and the inner wall of the molten pool 4 is a steel plate The welded structure or the welded structure of the steel plate lined with high-temperature anti-corrosion materials, the outside of the steel plate is coated with high-temperature anti-corrosion paint, the molten pool body is placed above the base 1, the bottom of the molten pool body is provided with a discharge valve 5, and the molten pool body is provided. One side of the pool body is provided with a roller rotati...
Embodiment 2
[0062] An on-line steel coating equipment including a coating device, comprising: a reduction cooling device, a coating device, and a cooling device after coating; along the incoming material direction, the reduction cooling device, the coating device, and the cooling device after coating are sequentially connected;
[0063] The reduction cooling device includes: material guide plate 27, sealing roller module, sealing roller and protective gas injection beam module, idler module, deflector 31, power feeding roller 32, idler roller and reducing gas injection beam module, rapid cooling Device 34, the front end of the reduction cooling device is provided with a guide plate 27, the rear end of the guide plate 27 is provided with a sealing roller module, the rear end of the sealing roller module is provided with a number of sealing rollers and protective gas injection beam modules, and the sealing roller and protective gas injection beam The back end of the module is provided with a...
PUM
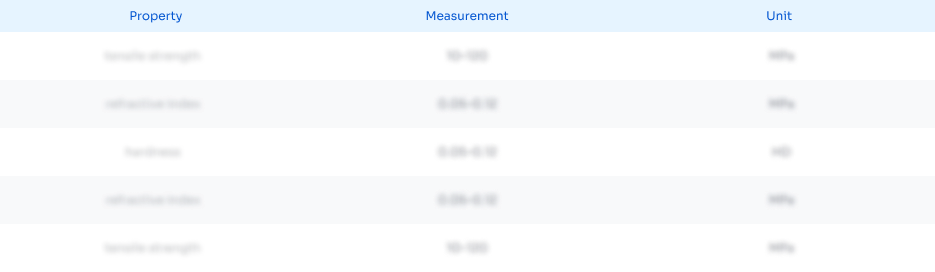
Abstract
Description
Claims
Application Information

- R&D
- Intellectual Property
- Life Sciences
- Materials
- Tech Scout
- Unparalleled Data Quality
- Higher Quality Content
- 60% Fewer Hallucinations
Browse by: Latest US Patents, China's latest patents, Technical Efficacy Thesaurus, Application Domain, Technology Topic, Popular Technical Reports.
© 2025 PatSnap. All rights reserved.Legal|Privacy policy|Modern Slavery Act Transparency Statement|Sitemap|About US| Contact US: help@patsnap.com