Larger titanium alloy structural component die-forging forming method
A technology of titanium alloy and structural parts, which is applied in the field of die forging of large titanium alloy structural parts, can solve the problems of high rib sagging and high rib filling difficulties, and achieve the effect of reducing the demand for maximum forming force
- Summary
- Abstract
- Description
- Claims
- Application Information
AI Technical Summary
Problems solved by technology
Method used
Image
Examples
Embodiment Construction
[0028] Describe in detail the implementation process of the inventive method below in conjunction with accompanying drawing:
[0029] (1) First, perform pre-forging on the blank 10 to obtain the pre-forging 3, wherein the pre-forging includes the following steps:
[0030] (1) The first pre-forging: see Figure 8 , the first pre-forging die 20 carries out the forging forming of the high-rib part 1 of the forging and the forming of the web lower die surface 2-1 of the pre-forging on the blank 10, and at the same time, the first pre-forging die 20 is located on the high-rib part 1 The upper die surface of the blank on the inner side is subjected to longitudinal split necking forming. During the split necking process, the metal material flows to the inner side of the high rib under the forging pressure of the first pre-forging die 20 and converges upward to form a boss 30. A concave groove 40 extending longitudinally is formed between the high-rib portion 1 and the boss 30, see ...
PUM
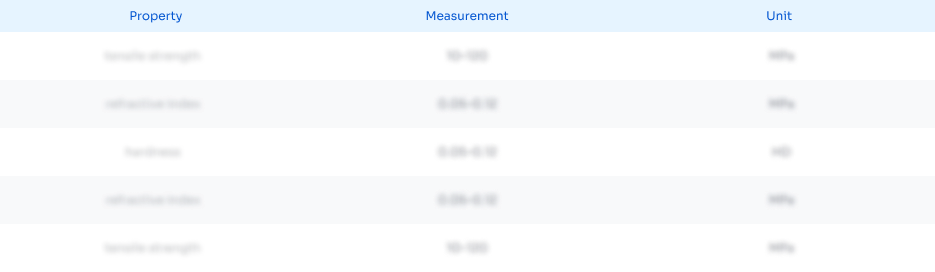
Abstract
Description
Claims
Application Information

- R&D
- Intellectual Property
- Life Sciences
- Materials
- Tech Scout
- Unparalleled Data Quality
- Higher Quality Content
- 60% Fewer Hallucinations
Browse by: Latest US Patents, China's latest patents, Technical Efficacy Thesaurus, Application Domain, Technology Topic, Popular Technical Reports.
© 2025 PatSnap. All rights reserved.Legal|Privacy policy|Modern Slavery Act Transparency Statement|Sitemap|About US| Contact US: help@patsnap.com