Manufacture process of thin-wall U-shaped bend pipe with small bending radius
A technology of bending radius and manufacturing process, which is applied in the field of manufacturing technology of thin-walled small bending radius U-shaped pipes, can solve the problems of reduced ball diameter, high cost, poor roundness, etc., and meet the requirements of ball diameter and production cost. Low, reduce the effect of deformation
- Summary
- Abstract
- Description
- Claims
- Application Information
AI Technical Summary
Problems solved by technology
Method used
Image
Examples
Embodiment Construction
[0015] Below in conjunction with the accompanying drawings, the present invention will be further described in detail by taking nickel-based φ38X4 pipe fittings to make a U-shaped (180°) elbow with a bending radius of R20 and requiring a ball diameter ≥ φ21.5 as an example.
[0016] The manufacturing process of the thin-walled U-shaped elbow with small bending radius includes the following steps: A) sand filling: filling the pipe with sand, such as brown corundum sand, and closing the two ports of the pipe with end caps; B) pre-bending :Such as Figure 1 to Figure 2 As shown, the pipe fitting 1 is installed on the top heading pipe bending machine: the top heading clamp 2 clamps one end of the pipe fitting 1, and the other end of the pipe fitting 1 is fixed by the pipe bending die 3 and the clamping block 4, and the pipe bending die 3 and the clamping block 4 are set There are matching arc-shaped grooves; the main shaft 5 drives the pipe bending die 3 to rotate, and at the same...
PUM
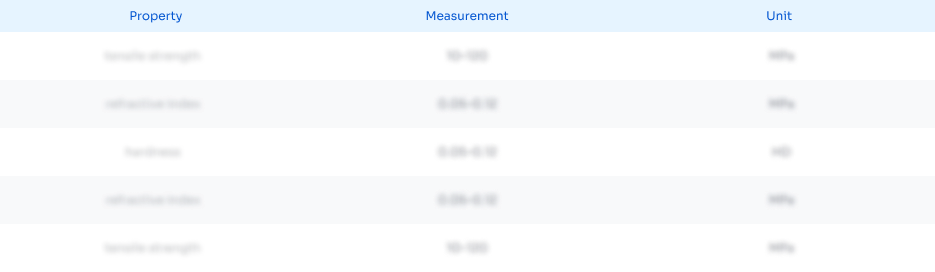
Abstract
Description
Claims
Application Information

- R&D
- Intellectual Property
- Life Sciences
- Materials
- Tech Scout
- Unparalleled Data Quality
- Higher Quality Content
- 60% Fewer Hallucinations
Browse by: Latest US Patents, China's latest patents, Technical Efficacy Thesaurus, Application Domain, Technology Topic, Popular Technical Reports.
© 2025 PatSnap. All rights reserved.Legal|Privacy policy|Modern Slavery Act Transparency Statement|Sitemap|About US| Contact US: help@patsnap.com