Fixed-bed low-carbon olefin catalyst, preparation method and use thereof
A low-carbon olefin and catalyst technology, which is applied in the field of fixed-bed preparation of low-carbon olefin catalyst, preparation and application thereof, can solve the problems of low selectivity of low-carbon olefin, poor strength, poor thermal stability, low CO conversion rate, etc. Reactivity, good thermal stability, and the effect of improving selectivity
- Summary
- Abstract
- Description
- Claims
- Application Information
AI Technical Summary
Problems solved by technology
Method used
Image
Examples
Embodiment 1
[0027] Weigh 48.0 grams of ferroferric oxide (Fe 3 O 4 ), 15.0 grams of manganese oxide (MnO), 15.0 grams of copper oxide (CuO), 10.0 grams of potassium oxide (K 2 O), 7.0 grams of cerium oxide (CeO 2 ) And 5.0 grams of antimony oxide (Sb 2 O 3 ) Six kinds of raw materials and 3 grams of carbon black powder with a weight percentage of 3% based on the total amount of raw materials, milled and mixed in a ball mill for 2 hours; based on the total amount of raw materials, 20 grams of 20% weight percent deionized water is added to the mill The kneaded material is kneaded to a soft shape; the kneaded material is fed into the extruding machine to form a strip with a diameter of 5mm, and cut into a column with a length of 20mm, after natural drying, it is sent to the drying equipment , Dried at 120°C for 8 hours for use; send the dried precursor into a high-temperature furnace, calcined at 1200°C for 6.0 hours, after cooling, crush and sieve into 60-80 meshes to obtain the required fixed...
Embodiment 2
[0029] Weigh 78.0 grams of ferroferric oxide (Fe 3 O 4 ), 6.0 grams of manganese oxide (MnO), 6.0 grams of copper oxide (CuO), 0.5 grams of potassium oxide (K 2 O), 0.5 grams of cerium oxide (CeO 2 ) And 9.0 grams of antimony oxide (Sb 2 O 3 ) Six kinds of raw materials and 3 grams of carbon black powder with a weight percentage of 3% based on the total amount of raw materials, milled and mixed in a ball mill for 2 hours; based on the total amount of raw materials, 20 grams of 20% weight percent deionized water is added to the mill The kneaded material is kneaded to a soft shape; the kneaded material is fed into the extruding machine to form a strip with a diameter of 5mm, and cut into a column with a length of 20mm, after natural drying, it is sent to the drying equipment , Dried at 120°C for 8 hours for use; send the dried precursor into a high-temperature furnace, calcined at 1600°C for 2.0 hours, after cooling, it is crushed and screened into 60-80 meshes to obtain the requir...
Embodiment 3
[0031] Weigh 19.0 grams of ferroferric oxide (Fe 3 O 4 ), 48.0 grams of manganese oxide (MnO), 8.0 grams of copper oxide (CuO), 24.3 grams of potassium oxide (K 2 O), 0.4 grams of cerium oxide (CeO 2 ) And 0.3 grams of antimony oxide (Sb 2 O 3 ) Six kinds of raw materials and 3 grams of carbon black powder with a weight percentage of 3% based on the total amount of raw materials, milled and mixed in a ball mill for 2 hours; based on the total amount of raw materials, 20 grams of 20% weight percent deionized water is added to the mill The kneaded material is kneaded to a soft shape; the kneaded material is fed into the extruding machine to form a strip with a diameter of 5mm, and cut into a column with a length of 20mm, after natural drying, it is sent to the drying equipment , Dried at 120°C for 8 hours for use; send the dried precursor into a high-temperature furnace, calcined at 800°C for 10.0 hours, and after cooling, it is crushed and screened into 60-80 meshes to obtain the ...
PUM
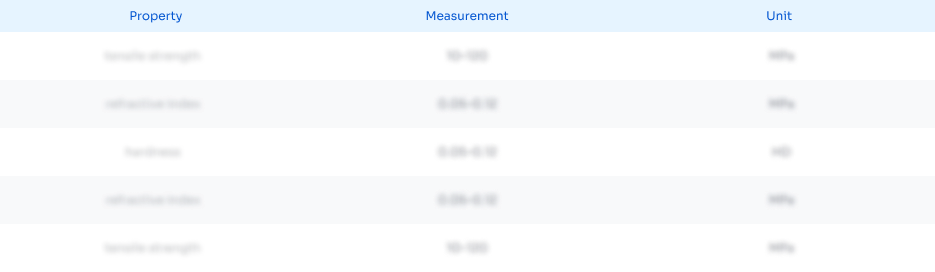
Abstract
Description
Claims
Application Information

- R&D
- Intellectual Property
- Life Sciences
- Materials
- Tech Scout
- Unparalleled Data Quality
- Higher Quality Content
- 60% Fewer Hallucinations
Browse by: Latest US Patents, China's latest patents, Technical Efficacy Thesaurus, Application Domain, Technology Topic, Popular Technical Reports.
© 2025 PatSnap. All rights reserved.Legal|Privacy policy|Modern Slavery Act Transparency Statement|Sitemap|About US| Contact US: help@patsnap.com