Reciprocating grate-fired furnace
A technology of reciprocating grate and layer burning furnace, which is applied in the direction of combustion chamber, combustion method, combustion equipment, etc., to achieve the effect of easy maintenance, reduction of heating area, and reduction of production cost
- Summary
- Abstract
- Description
- Claims
- Application Information
AI Technical Summary
Problems solved by technology
Method used
Image
Examples
Embodiment Construction
[0017] The present invention will be described in further detail below in conjunction with the accompanying drawings.
[0018] Such as figure 1 As shown, the present invention includes a body of furnace 1, a coal hopper 2, a front arch 6, a rear arch 7, a fire grate 8 and a gate 9, wherein the top of the body of furnace 1 is a boiler 3, and the bottom is a combustion chamber 5. A flue 4 is formed between the 3 and the combustion chamber 5; An opening is provided on the inner wall of the furnace body 1 on one side of the combustion chamber 5, and the coal hopper 2 is arranged outside the opening. The front arch 6, the rear supply 7 and the fire grate 8 are arranged in the combustion chamber 5, wherein the front arch 6 is located Above the opening, one end of the rear arch 7 is affixed to the inner wall of the other side of the body of heater 1, and the other end is a free end, located between the opening and the front arch 6, and the free end is connected to the side of the bo...
PUM
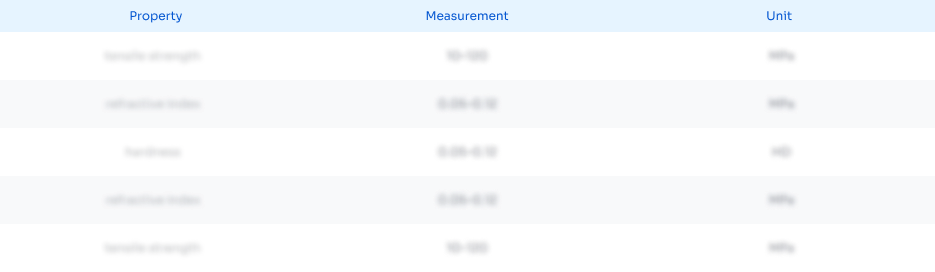
Abstract
Description
Claims
Application Information

- R&D
- Intellectual Property
- Life Sciences
- Materials
- Tech Scout
- Unparalleled Data Quality
- Higher Quality Content
- 60% Fewer Hallucinations
Browse by: Latest US Patents, China's latest patents, Technical Efficacy Thesaurus, Application Domain, Technology Topic, Popular Technical Reports.
© 2025 PatSnap. All rights reserved.Legal|Privacy policy|Modern Slavery Act Transparency Statement|Sitemap|About US| Contact US: help@patsnap.com