Method for improving excessive circuit etching of circuit board
A circuit board and etching technology, which is applied in chemical/electrolytic methods to remove conductive materials, printed circuits, printed circuit manufacturing, etc., can solve problems such as excessive etching, spray pressure changes, etc., to prevent excessive circuit etching and pH value Optimize and improve the effect of line refinement
- Summary
- Abstract
- Description
- Claims
- Application Information
AI Technical Summary
Problems solved by technology
Method used
Examples
Embodiment 1
[0026] Use gantry electroplating to electroplate 5-6 μm of copper on the surface of the clean and dried circuit board. Then apply the dry film according to the following steps: feeding (checking the quality of the incoming circuit board surface)→cutting the film→applying the dry film→receiving the board (checking the quality of the circuit board surface after the film is applied); the process condition of the film is temperature: 105 ℃; pressure: 2.0-5.0kg / cm 2 ;Speed: 3.0-4.0m / min. Exposure in the exposure process, the exposure process conditions are temperature: 20±2°C; vacuum pressure: ≤-680mmHg; exposure scale: 7 grids. Then develop, the developing conditions are temperature: 30±2℃; upper and lower pressure: 1.2±0.2kg / cm 2 ; Speed: 2.6±0.2m / min; Time: 10-15s; After washing and drying, the etching area of the electroplated copper layer is covered by dry film, and the required copper lines are exposed, and the exposed copper lines form a circuit pattern. The width of th...
Embodiment 2
[0028] Use gantry electroplating to electroplate 5-6 μm of copper on the surface of the clean and dried circuit board. Then apply the dry film according to the following steps: feeding (checking the quality of the incoming circuit board surface)→cutting the film→applying the dry film→receiving the board (checking the quality of the circuit board surface after the film is applied); the process condition of the film is temperature: 105 °C; Pressure: 3.0kg / cm 2 ;Speed: 3.5m / min. Exposure in the exposure process, the exposure process conditions are temperature: 20°C; vacuum pressure: ≤-680mmHg; exposure scale: 7 grids. Then develop, the developing conditions are temperature: 30°C; upper and lower pressure: 1.2kg / cm 2; Speed: 2.6m / min; Time: 13s; After washing and drying, the etching area of the electroplated copper layer is covered by a dry film, and the required copper lines are exposed, and the exposed copper lines form a circuit pattern. The width of the copper lines 0.035...
PUM
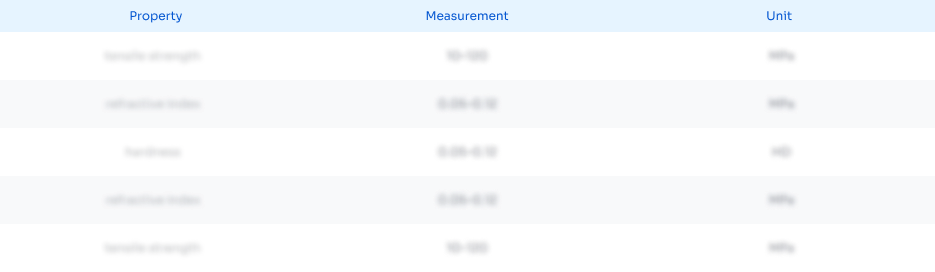
Abstract
Description
Claims
Application Information

- R&D
- Intellectual Property
- Life Sciences
- Materials
- Tech Scout
- Unparalleled Data Quality
- Higher Quality Content
- 60% Fewer Hallucinations
Browse by: Latest US Patents, China's latest patents, Technical Efficacy Thesaurus, Application Domain, Technology Topic, Popular Technical Reports.
© 2025 PatSnap. All rights reserved.Legal|Privacy policy|Modern Slavery Act Transparency Statement|Sitemap|About US| Contact US: help@patsnap.com