Hydraulic sand jet perforation choke manifold
A throttling manifold and hydraulic jet technology, applied in the production fluid, wellbore/well components, sealing/packing, etc., can solve problems such as gate valve erosion damage, inability to accurately control casing pressure, etc. corrosion, improve perforation efficiency, and facilitate replacement
- Summary
- Abstract
- Description
- Claims
- Application Information
AI Technical Summary
Problems solved by technology
Method used
Image
Examples
Embodiment 1
[0019] Since the existing choke manifold cannot accurately control the casing pressure during hydraulic sandblasting perforation, and the gate valve is severely damaged by the erosion of the sand-carrying fluid, in order to overcome the above problems, the embodiment provides a hydraulic sandblasting Special choke manifold for perforation.
[0020] Such as figure 1 As shown, a hydraulic sandblasting and perforating throttling manifold includes a first four-way pipe 13 and a second four-way pipe 14. The first slab gate valve 7, the third slab gate valve 9 and the fifth slab gate valve 11 are arranged side by side between them; the first slab gate valve 7 and the fifth slab gate valve 11 are located on both sides of the third slab gate valve 9.
[0021] A first fixed throttle valve 1 is provided between the end of the first flat gate valve 7 connected to the first pipeline cross 13; the end of the fifth flat gate valve 11 connected to the first pipeline cross 13 A fourth fixed...
Embodiment 2
[0029] On the basis of embodiment 1, the application mode of the present invention is:
[0030] (1), first connect the manifold inlet 5 with the wellhead casing gate valve;
[0031] (2), open the first flat gate valve 7, the second flat gate valve 8, the fourth flat gate valve 10, the fifth flat gate valve 11, and close the third flat gate valve 9;
[0032] (3) Test the throttling pressure, perform tubing pumping according to the perforation displacement requirements, and test the casing pressure. If the casing pressure is lower than the design pressure, close the first flat gate valve 7, the second flat gate valve 8, and the second flat gate valve as required. Any one or more of the four slab gate valves 10 and the fifth slab gate valve 11 until the casing pressure reaches the design requirement.
[0033] (4) If the casing pressure is greater than the design pressure, stop pumping, and replace any of the first flat gate valve 7, the second flat gate valve 8, the fourth flat ...
PUM
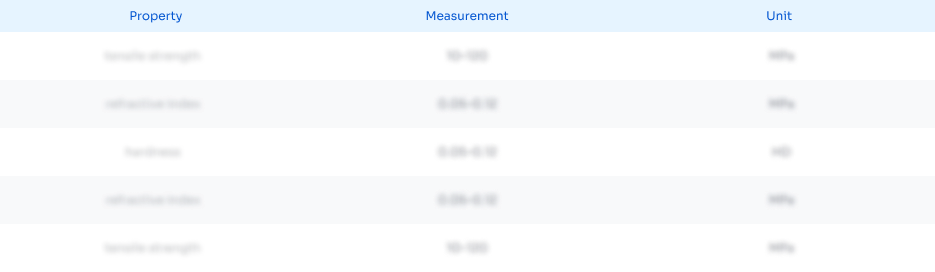
Abstract
Description
Claims
Application Information

- Generate Ideas
- Intellectual Property
- Life Sciences
- Materials
- Tech Scout
- Unparalleled Data Quality
- Higher Quality Content
- 60% Fewer Hallucinations
Browse by: Latest US Patents, China's latest patents, Technical Efficacy Thesaurus, Application Domain, Technology Topic, Popular Technical Reports.
© 2025 PatSnap. All rights reserved.Legal|Privacy policy|Modern Slavery Act Transparency Statement|Sitemap|About US| Contact US: help@patsnap.com