Lathe precise machining method for ultrathin-wall-thickness metal pipe part
A tube parts, precision machining technology, applied in the field of lathe precision machining of ultra-thin-walled and thick metal tube parts, can solve the problems of low processing yield, poor stability, large deformation, etc., and achieve strong targeted effects
- Summary
- Abstract
- Description
- Claims
- Application Information
AI Technical Summary
Problems solved by technology
Method used
Image
Examples
Embodiment Construction
[0027] Below in conjunction with accompanying drawing and embodiment the specific embodiment of the present invention is described in further detail:
[0028] figure 1A schematic diagram of a thin-walled pipe part used as an example of the present invention is given. The overall structure is a thin-walled structure, and one end is a flange structure. The ratio of the pipe diameter to the wall thickness in the overall structure is 130. A lathe precision machining method for ultra-thin wall thickness metal pipe parts of the invention comprises the following steps:
[0029] Step 1: It is the blank preparation stage, specifically, first select a round bar with an outer diameter larger than the maximum outer diameter of the final part, and process it into such as figure 2 The rough blank 5 shown; the rough blank 5 is subjected to a high-temperature treatment process, and then the heat-treated rough blank 5 is processed to a profile that is basically similar to the requirements of...
PUM
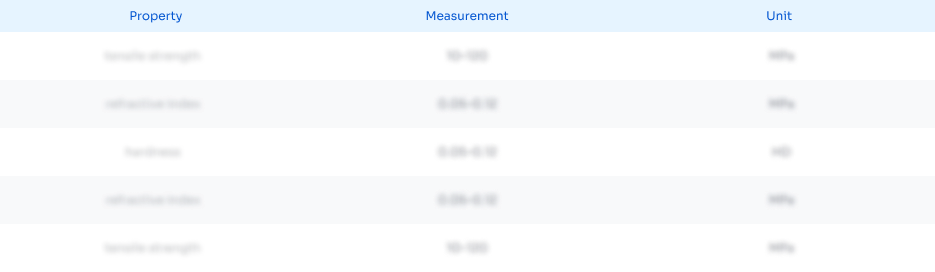
Abstract
Description
Claims
Application Information

- R&D
- Intellectual Property
- Life Sciences
- Materials
- Tech Scout
- Unparalleled Data Quality
- Higher Quality Content
- 60% Fewer Hallucinations
Browse by: Latest US Patents, China's latest patents, Technical Efficacy Thesaurus, Application Domain, Technology Topic, Popular Technical Reports.
© 2025 PatSnap. All rights reserved.Legal|Privacy policy|Modern Slavery Act Transparency Statement|Sitemap|About US| Contact US: help@patsnap.com